Fire it Up
Now comes the fire. P-Tex fumes aren’t the sort of thing you want to inhale, so set up in a well ventilated area or open a window. Move the flame of your lighter so that the tip of the flame contacts the tip of the P-Tex candle. After a few seconds, the flame will envelope the candle, set it alight, and the candle will start to melt and drip. The first several drops of P-Tex will include a bit of byproduct build up – black flecks that you don’t want to drip in the repair itself. To burn off this initial byproduct, start by holding the P-Tex candle over a scraper tool, a scrap piece of wood, or piece of foil you’ve set on the ski, next to the damaged area. After those first initial drips have landed on your wax scraper or piece of wood, you’re ready to move the candle over to just above the damaged area of the base and begin filling it.
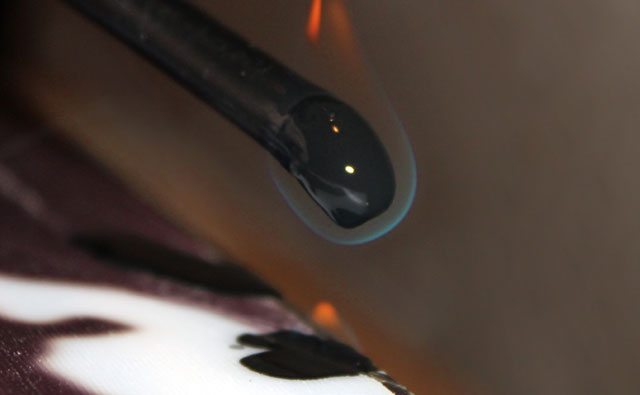
It is very important to keep the tip of the P-Tex candle at the lowest possible temperature while it’s burning and dripping material into the gouge, for two reasons:
- If the flame gets too hot, the chemical properties of the burning P-Tex change, producing unwanted byproducts. These byproducts are often visible as those same black flecks in the drips and/or tip of the candle (white or clear P-Tex becomes advantageous in this way, since you can more clearly see those black flecks). These byproducts cause the melted P-Tex to become more brittle when it hardens, because they physically interfere with the P-Tex’s chemical structure.
- As the P-Tex candle heats up, it becomes less dense (and softer) and therefore more susceptible to thermal expansion. In other words, the hotter the P-Tex gets during the repair, the more likely it is to expand and contract with future temperature swings, making it more likely to crack and fall out.
(For a better understanding of the chemical changes that occur to P-Tex during combustion, and how those changes can affect the quality of a repair, a primer on P-Tex and polymer chemistry can be found at the end of this article.)
There are two ways to control the heat of the burning P-Tex candle:
- Keep the tip of the P-Tex candle as close to the ski as possible. If the flame on the P-Tex candle turns red or orange, it is getting too much oxygen and burning too hot. The flame should ideally be blue.
- Slowly spin the P-Tex candle as you drip the P-Tex into the gouge. Don’t spin it so fast that the flame goes out, but don’t spin it so slowly that it is not cooling the tip. Both of these techniques take a bit of practice.
As the P-Tex drips off the candle, allow it to fill in the gouges on your equipment.
Drip more into the gouge than you think you will need, as the P-Tex will shrink slightly as it cools, gouges are usually deceptively voluminous, and we’ll scrape away any excess material. Once the damage is sufficiently filled, blow out the P-Tex candle and allow the ski to sit for at least 10 minutes while the P-Tex cools.
NEXT: SCRAPE, THEN SHRED
From my personal experience – TOKO Base Repair Powder is much-much better than burning candles (requires hot Iron, so for indoor use only)
Couple things:
1) You make no mention of wearing a mask or having proper airflow while doing p-tex repair. Although it probably won’t kill you, breathing p-tex fumes is very bad for your health.
2) Most P-Tex candles, although better than doing nothing, are not designed for “core shot” type repairs. For this, there are a bunch of other products and techniques to increase the chances of it holding. Your standard P-Tex candle is NOT the BEST tool for the job.
Jeff: Good point about ventilation. I always wondered why one of your eyes twitched whenever you hear George Michael songs. P-tex fumes are something to be avoided in large quantities and I know just speaking for myself, I’d never want to ruin the pleasure of my Wham vinyl collection. It’s just too risky and I feel bad you’ll never be able to enjoy “Careless Whisper” like you once did. But I think most people will realize some breathing room is a good thing as soon as that candle fires up.
As far as size of repairs being dealt with via candles…it just depends on the repair. I’ve filled plenty of core shots with candles and have never had one rip out. (So have lots of other people…for years). Sure extruders/base patches/repair guns might be needed if it’s a bad one but candles are cheap and it’s worth trying before dropping more money in a shop. There’s no ‘given’ that a candle repair won’t work.
Nice write up Sam!
Thanks for the comments, Jeff, and you’re right—we’ve added a word about ventilation. As for wearing a mask, certainly if you are using high-fluoro waxes and either waxing or dropping hot p-tex on there. But if you don’t use high-flouro waxes (like 99% of the population who aren’t racing), then working in a well ventilated area or opening a window—especially for the “smaller than a quarter” sized repairs this article addresses—is a good practice.
Great article and this brings me back to my days of doing all my own base repairs. Good tips and this will get the job done for sure. This will also help people realize just how easy it can be with a little instruction. Thanks Blister
You state that a red or orange flame is getting too much oxygen and burning too hot and that ideally the flame should be blue. A blue flame would actually be hotter and using more oxygen than a red/orange flame and presumably is better because it is burning cleaner. A flame giving a red/orange colour suggests that there is unburnt or partially burnt material in the flame and these could be responsible for the black flecks you then find in the repair.
Neil, you are definitely correct. The blue flame will be the hottest part of the flame while a red/orange flame will not be as hot. The red / orange color is typically a sign of partial / incomplete combustion. The wording in the article is perhaps a bit misleading so let me try to clear it up here.
The idea with holding the tip of the candle as close to the base as possible (and slowly spinning the candle as well) is to control the rate of oxygen transfer to the flame more than to control the temperature. By controlling the rate of oxygen transfer to the reaction, we can also control the rate at which the hydrocarbons (and additives) are combusted. When the flame gets more oxygen, (ie, you move the candle from the base or stop spinning the tip) oxygen is no longer the limiting reactant in the combustion. What limits the combustion then begins to be the availability of hydrocarbon. When oxygen is no longer the limiting reactant the flame has a tendency to spread out in a sense. It is looking more material to burn because now it has enough oxygen. It begins to burn in a less controlled manner, though not technically hotter than the blue flame, but the candle is exposed to more heat overall. You only want to be liberating the polymer at the tip of the candle. When the flame tries to consume more hydrocarbon than it has oxygen for, you get partial combustion and small black flecks in the repair that are by products of combustion. By keeping the combustion localized to the tip, you get more complete combustion and a cleaner repair.
I know that isn’t the most complete explanation, the process is actually fairly complex and involves a decent amount of chemistry. Let me know if you still have questions though, and I apologize for the vague wording in the article!
-Sam
Sorry Sam the chemist in me couldn’t help commenting. Thanks for clarifying.
Thanks for the info. I’ve never concentrated on spinning the candle before. Repairs will be better in the future.
A drip p-tex candle is the wrong way to repair an edge core shot. Those candles don’t stick to fiberglass or the metal edge, It will probably rip out the next day You need something to bond the ptex to the base fiberglass and metal edge, epoxy or metal grip is the only way to make it a permanent bond between the surfaces.
Keeping the burning candle as close to the repair as possible is to minimize carbon buildup, a blue flame is hotter because it’s a controlled amount of oxygen. When fire gets more oxygen than it needs it wants to spread out to grow and consume more combustible material. That why it’s large and orange/red. You don’t want to minimize the temperature of the candle but get it as hot as possible to burn clean and efficiently (reduce carbon) and to keep the ptex drip molten while it somewhat bonds to the ptex base.
A ptex drip candle is only effective on a non core shot where the original base is still in tact, and even then it’s unlikely that it will become a permanent bond, most likely have to fix it on a yearly bases if it’s a decent size chunk. Get a core shot at the hill, fix it to prevent water damage with a drip candle then get it fixed properly when you have the opportunity.
Hey Ryan, thanks for your comment.
You’re correct that large base repair is better done with other techniques. The idea with this article is to get the reader familiar with the ptex candle because it is a cheap and easy fix that can solve some (not all) issues. It’s easily accessible to the average skier.
For the note on flame temperatures, you can read my response to Neil above. The concept is just a bit above a 101 article, hence the simplified explanation in the article. Thanks for your feedback!
I’ve always found that for deeper gouges, filling in one go (this article is unclear about how many layers to apply) tends to lead to weak repairs. The heat of a large glob of ptex makes for a brittle repair, and I’ve even seen big fills burn until put out.
It’s far better to apply several thin layers, with a few minutes between applications. Also, to avoid pulling out a fresh base repair, scrape from the center of the patch out one way, then the other.
A final note-ptex from a candle functions like extruded (rather than sintered) base material and isn’t as strong. For core shots, the epoxy fortified ptex sticks a base welder uses yield a MUCH stronger repair.
Hey everyone, after four terrible years of skiing on rocks in tahoe I’ve come up with an edge core shot method I’m psyched about. After trying base welds, Ptex dripping, and even jb weld, the reap airs would still only hold up a week or so. I started making my own flat strips of ptex by smashing a candle with an iron between parchment paper. Once you have a good strip roughly the same thickness as the base, cut it to fit snugly into the exposed core/edge shot. Superglue it into place. Next, use two layers of parchment paper and iron over it until it is flush with the base and edge. Let it cool, then SLOWLY peel off the paper. Voilá!
Base welds would only hold up for a few days on this damage for me, dripping even less. The last one I put in was six inches long and a centimeter wide directly underfoot along my edge. I’ve been skiing over rocks and dirt and in the park the last two weeks and it is holding up better than any shop repair so far. Without burning the ptex, it remains flexible, and tough. Even a metal scraper can’t smooth it out, I use a sharp razor blade. Not the prettiest way to fix your core shots along the edge, but it’s the most durable and cost effective method I have found.
I’ve read elsewhere that typical glue guns shouldn’t be used with P-tex because, while they can melt the candle, they are not hot enough to make a durable repair. But this article calls for temperatures as low as possible. I have an industrial glue gun (for gluing corrugated cartons). Can I use it for P-tex or no?
Hey Brett,
I definitely can’t condone you potentially sacrificing your glue gun with a base repair, but I can clarify a bit on the temperature issue.
This article is written from the perspective of burning P-Tex candles, because of that, not all of the concepts are explained in a generalized sense. In general, we want to achieve 1) good integration of the repair with the existing base and 2) minimally change the properties of the P-Tex repair in the process.
For burning P-Tex candles, we achieve this with a clean wound, warm base and controlled combustion at the candle tip. Controlled combustion is not exactly analogous to temperature. Uncontrolled combustion (orange flame) leads to chemical byproducts — short hydrocarbons, radicals, reactive species, etc. These byproducts are what change the level of crystallinity and cross linking in the polymer — not directly temperature.
But in general, we achieve (1) with high temperature and (2) by being chemically “gentle” to the polymer.
It turns out, the way you heat up the P-Tex is quite important. Lighting it on fire can lead in to partial combustion and byproducts — bad. Glue gun style devices use resistive heat and don’t rely on a chemical reaction at all — good. Base welds and P-Tex guns heat the P-Tex up to pretty high temperatures but because there is no combustion, the P-Tex stays chemically intact (more or less) and is stronger. The higher temperature the P-Tex, the lower viscosity (good for getting into nooks and crannies) and the better chemical integration with the existing base.
Recap: High temperature is good, uncontrolled combustion is bad.
Circling back to your question, I doubt your glue gun would get hot enough to create a good repair, it might have a hard time melting the P-Tex at all and that could result in a big mess. Use at your own risk.
Hopefully that answers your question. Every time I revisit this article the topic gets more and more nuanced, it’s a simple problem that has a lot of chemistry, material science and engineering behind it!
Thanks,
Sam
Thank you for the thorough explanation, Sam. Armed with that information and some ideas gleaned elsewhere, here’s what I did to achieve a successful repair (so far) on a bad base blister (overheated while waxing):
After de-waxing the affected area, I sliced an oval-shaped slit in the bubble, heated with heat gun and clamped it flat with thick steel plates. When cooled, I trimmed the perimeter of the slit using the “keystone” method, creating an inward bias to help lock in the P-Tex. I then glued in a thin piece of cotton to absorb some of the melted P-Tex and add grip. Once that was set, I lit the candle using a butane torch and held it close to the wound until it was filled. I filed off the excess with a fine rasp, followed by sandpaper.
For added insurance, I then traced the perimeter of the repair with an old soldering gun, smoothing the joint between the base and the P-Tex. Followed again with some more sanding and a final wax.
It was a lot of work but I’m impressed by how well it came out.
Wow, that sounds like a brutally hard way to do a large patch, and in the end it’s still soft/extruded material.
Next time try a linoleum knife, some epoxy, and one of these: http://www.race-werks.com/base-repair-kit/
I think the key concept missing here is that candles aren’t (pure) P-Tex. They’re a blend of P-Tex with paraffins and probably some other lower-molecular-weight hydrocarbons to make them burnable. The temperature required to melt/ignite a candle is different from the temperature required to melt pure UHMWPE, and as Sam says in his reply you have to worry about undesirable combustion byproducts like soot when you’re dealing with a candle.
Hot glue guns come in varying temperatures and powers. Guns designed to melt industrial “high-temperature” adhesives (say, a SureBonder Pro2-220) are perfectly capable of melting P-Tex, but those aren’t really much cheaper than a dedicated “P-Tex gun”. Also, purpose-built base repair guns have wide, flat tips with separate lower-temperature heating elements to both shape/pressure the patch and preheat the area around it for better bonding. Search for “Base Mender RP350” for a typical example.
I realize this article is really old, but want to address a couple points:
w.r.t. solvents, Isopropyl Alcohol (IPA) and water don’t dissolve waxes or similar contaminants that often find their way into damaged areas. You could use a 2-step approach with mineral spirits to get rid of the heavy oil/wax-ish stuff followed by IPA, but I think that the orange-oil solvents that Swix/Toko/SVST/etc sell and that are available much more cheaply at home-improvement stores are easiest overall.
Another “beginner-level” alternative to candles is to use pure UHMWPE welding wire and a low-temperature “plastic-soldering iron”. Tognar sells a nice iron for $25 or so, which is what I’ve used for small/superficial repairs for the last ~15 years. Drip candles are mixed with very soft paraffin to make them burn, so using pure wire yields a significantly stronger repair. The iron also provides a lot more fine control over the process, and makes it easier to simultaneously heat the repair area, which is a key to good bonding.
There is a fundamental problem with both candle and iron repairs (and also base welds for that matter): The resulting repair material is the equivalent of old-school extruded base material. Even if you start with sintered repair media, the act of melting it into the damaged area destroys the microstructure, leaving a softer material that doesn’t take wax, has reduced impact resistance, and will steadily “erode” if you ski aggressively on hard snow. Finally, the repair material doesn’t stick very well to core or edge material.
All of these issues can be addressed by creating an inlay patch, which is the same process that reputable shops use when rebuilding the base above an edge or sidewall repair. The process is actually quite simple: Cut and peel out a regularly-shaped section of your base. Cut out an identical “puzzle piece” from a sheet of sintered, flame-treated base material (available from SVST, Tognar, etc). Epoxy the patch into the hole in the base with moderate pressure (I aim for 50-100 lbs per square inch of patch) using a slow-curing, flexible epoxy like Hysol 608 or 11C. The result is equivalent to the “die-cut” bases on a lot of skis, and it’s “as good as new” in most respects. The fact that the patch material is flame-treated on the back allows epoxy to bond to it, which is the key to getting your repair to stick to exposed core or edge.
Regardless of which method you use, you can get raw materials easily from places like Race-Werks and Tognar Toolworks. Race-Werks is the retail arm of Sun Valley Ski Tools, and that’s probably where your shop is buying the stuff you’re getting from the techs on the DL to begin with.
I’m not sure what I was thinking when I said “IPA won’t dissolve paraffin”. It will.
I’ve had less luck with harder, plasticized waxes though.
One more remark: You mentioned metal-grip, and that’s a reasonable choice for a core shot if you must do a “liquid” repair for some reason. There are caveats though:
Metal-grip (henceforth “MG”) is quite a bit gummier than straight P-Tex, and it can be really hard to work the surface of an MG repair flat. The resulting surface also doesn’t wear as well as P-Tex. Skilled techs can get around by building up a thin base layer of MG against the base of the ski, and then layer regular P-Tex on top of that. If you’re really good with a base-repair iron you can melt the two layers together without actually mixing them, and the results can be very impressive.
I don’t have that level of iron-fu, so I’ll usually do an inlay patch repair (the “cookie-cutter” approach that I outlined in another comment) in that situation. It takes longer (a shop would charge ~2x as much for for a patch vs an MG weld, and the cost is almost entirely labor either way), but the result is bombproof.