Revel RW30 wheels
Build:
- Industry Nine Hydra hubs (Boost, SRAM XD driver)
- Sapim D-Light spokes (28)
- Sapim Black Brass nipples
Measured Internal Rim Width: 29 mm
Measured External Rim Width: 35 mm
Stated Weight (as built): 1840 grams
Blister’s Measured Weight:
- Front: 859 grams
- Rear: 981 grams
- Total: 1840 grams
MSRP (as built): $2200
Bolted to: Yeti SB5.5
Reviewer: 5’10” 180 lbs
Test Locations: Colorado Springs, CO
Test Duration (so far): ~110 miles / 12 rides
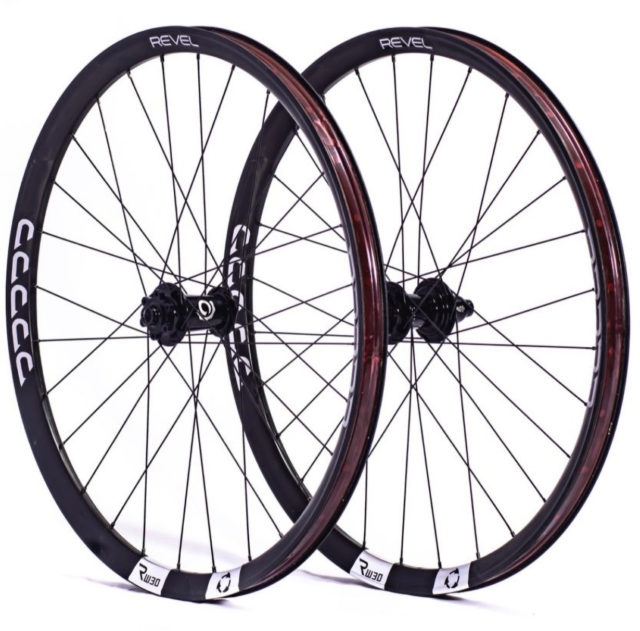
Intro
I don’t think I am alone in being a bit of a carbon-fiber skeptic. Many riders cite impact resistance, durability, production inefficiency, overall cost, and / or the relative inability to recycle it as reasons to not use carbon fiber on their mountain bikes.
That said, the bike world at large seems to have settled on carbon fiber as being an indispensable material long ago, and with good reason. There are clear and indisputable performance and weight benefits to carbon. It’s not a coincidence that carbon-fiber options rule the high-end bike frame and wheel markets. But even with the clear performance benefits of carbon, many carbon wheels released in the last ~two years have been attempting to address a few of the shortcomings listed above.
Revel Bikes out of Carbondale, Colorado is trying to go one further (or two or three… keep reading). Like many brands, Revel wanted to build a better, more durable wheelset made from carbon. But rather than follow the pack, Revel went a different direction with their raw materials and manufacturing, discovering some other unique attributes along the way.
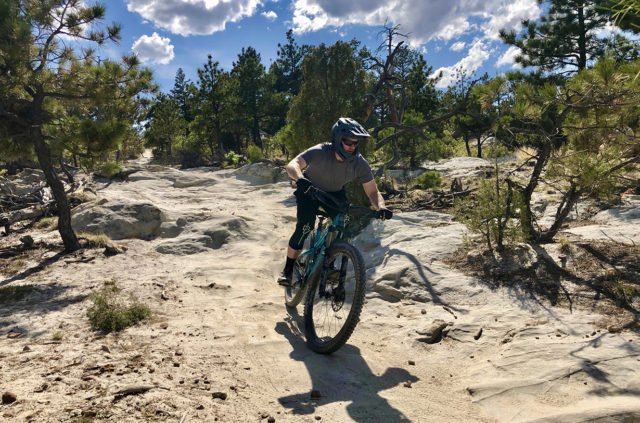
I now have a dozen rides on the Revel RW30 wheelset and think there are a number of reasons why these wheels — and the materials and processes used to produce them — warrant attention.
And in case you missed it, we posted a conversation with Revel founder, Adam Miller, on our Bikes & Big Ideas podcast where he delved into his very interesting and uncommon backstory in the bike industry, and we’ll also be posting another conversation with Adam on our GEAR:30 podcast this Friday where he discusses the whole story behind Revel’s wheels, so stay tuned for that. Finally, later this summer, we’ll post a long-term update on the RW30 wheels after reviewer Eric Freson and I have spent more time on them. But for now, let’s just dive into these unique wheels:
Traditional Carbon Fiber vs. Revel’s “Fusion-Fiber”
To understand how Revel went in a different direction than other brands, you first have to understand the standard carbon fiber traditionally used for bike frames and components.
Thermoset pre-preg carbon is a raw material that uses carbon-fiber filament as a reinforcing agent and is impregnated with epoxy resin. This raw material ships from materials manufacturers to product manufacturers requiring — dependent on the length of storage prior to actually using the material — rather burdensome temperature and contaminant controls.
To produce a bike part, pre-preg carbon is cut and laid by hand into a jig and then pressed, heated, and cured into the required shape. This shaping and curing can happen in slightly different ways depending on the manufacturer, but the basic premise is the same. (Researching this topic, I found that timeframes for curing vary, though Revel uses 45 minutes as a comparison benchmark for thermoset carbon). The excess cured material is then cut away from the final product and then the product itself is sanded and sealed using clear coat, primer, and / or paint.
That’s the basic gist of thermoset composites, which make up the majority of carbon-fiber products you see in the bike market. But as you have likely realized by this point, the Revel RW30 rims aren’t made from thermoset composites.
Enter thermoplastics. A decade ago while on a ride and early in his bike-industry career, Adam Miller met one-time ENVE Composites’ Vice President of Operations, Joe Stanish. Joe went on to become a co-founder and Chief Operating Officer for CSS Composites in Utah. Last year, Joe approached Adam about a reportedly revolutionary thermoplastic material CSS had developed called Fusion-Fiber, and specifically, its applicability in making bike wheels. Here’s what Revel says about Fusion-Fiber:
“Fusion-FiberTM is the name for this technology, which encompasses the material and the process … At a basic level, the crew at CSS removed all epoxy from standard pre-preg carbon and replaced it with advanced polymers – think nylon, but on a whole new level. The raw material is a blend of unidirectional long fiber German and Japanese carbon impregnated with this polymer. In its raw form, it is completely stable, has an unlimited shelf life, doesn’t need to be stored in a refrigerated room like standard epoxy prepreg carbon,”
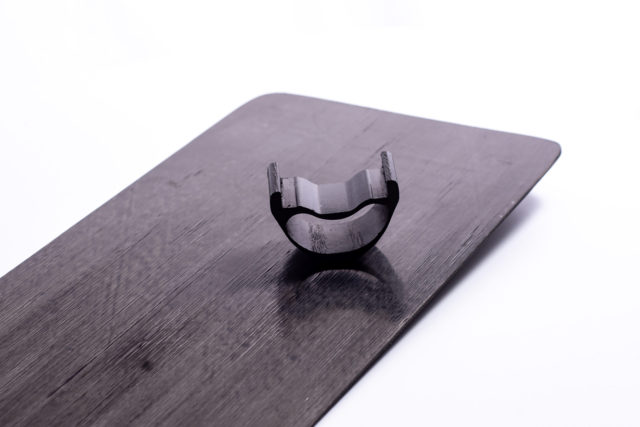
That’s the material itself. But as you just read, Fusion-Fiber isn’t just a material, it’s also a process. Here’s what Revel says about that process:
“Besides the material, the manufacturing process is where things get really crazy. The rims are laid-up and cross-plied robotically, leaving no space for human error or inconsistencies. The rims are then flash welded together, with an exponentially faster cure time than current rim technology so cure times go from around 45 minutes for a standard thermoset carbon rim to 20 seconds with this system, in a completely controlled environment so every rim comes out the same, every time. When the rim pops out of the mold, there is no epoxy resin to be scraped or sanded and it needs no clear coating.”
Revel goes on in their marketing copy to claim that Fusion-Fiber is stronger and more impact resistant than standard carbon fiber. They also say that nylon is more flexible than epoxy, so the Fusion-Fiber wheel has a quieter, more damped ride feel than standard carbon. They also claim that, in the event that a rim crack does happen, it’s far more likely to stay localized within a small section of the rim, rather than propagate as a crack tends to in standard carbon fiber. In short, the claim is that wheels made from Fusion-Fiber are better than standard carbon fiber in terms of both impact resistance and ride feel, while still retaining all the performance and weight benefits of standard carbon fiber.
If this is starting to sound like a Sham-Wow infomercial, my apologies, because wait, there’s more!
Due to the use of their polymer rather than epoxy resin as the binding agent for the carbon fibers in the pre-preg, Fusion-Fiber is considerably more recyclable than standard carbon fiber. Contrary to common knowledge, standard carbon fiber can actually be recycled through processes called pyrolysis or solvolysis. Essentially, the epoxy in thermoset carbon fiber is either burned away (pyrolysis) or stripped away using a solution (solvolysis). These processes are just as intensive as they sound from a labor and chemical perspective. They are also quite harsh on the carbon fibers in the material itself. This is why many carbon parts end up in a landfill, rather than being recycled.
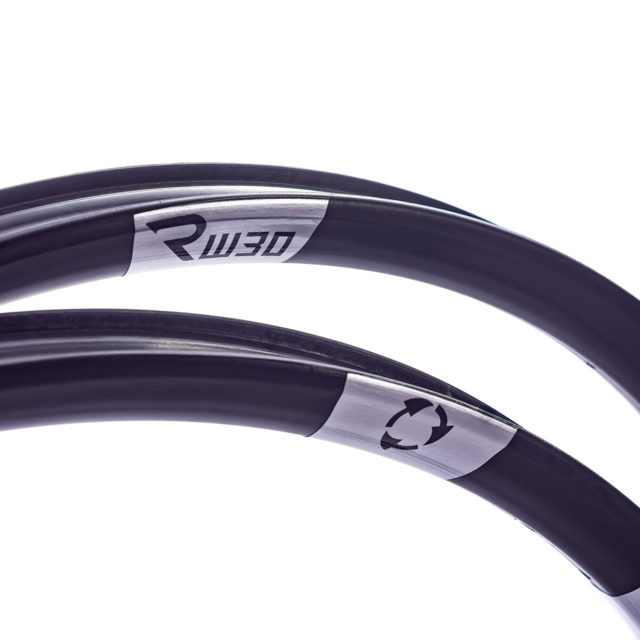
In contrast, Fusion-Fiber is different in that it can be recycled much more easily, and CSS Composites controls the recycling process in-house. In effect, rims no longer in use are chipped into 1-inch blocks and can then be melted and reformed into a new part. This does limit the size of the product that can be made from the recycled rim (due to the shorter, cut fibers) and Adam says that for now, the products from recycled Fusion-Fiber will be small. Revel recently announced on our Bikes & Big Ideas Podcast that they had made their first product, a tire lever, from recycled Fusion Fiber. Revel will also pay for the shipping if / when your Revel rim is severely damaged and therefore should be recycled (more on the warranty below).
If you’re reading this section and thinking that these claims are pretty extraordinary, you aren’t alone. Revel is claiming some pretty ambitious improvements to the standard carbon wheelset as a result of using Fusion-Fiber.
Rim Construction and Features
Talk of space-age materials and processes aside, from a shape and size perspective, the RW30 rims actually look pretty normal. They measure 29 mm wide internally and 35 mm wide externally, and are formed into a standard double-wall design with the now ubiquitous hookless bead.
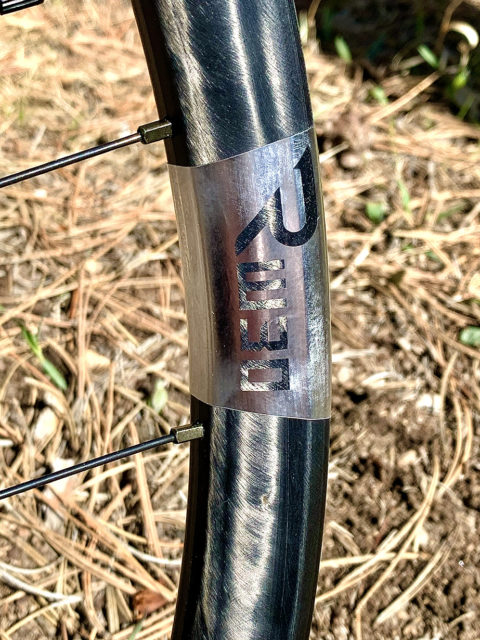
The RW30 wheels come installed with rim strips and a standard tubeless Presta valve. The rim’s finish is raw black with silver decals. Other than seeing the fibers in the material itself in the right light, the RW30 is about as traditional as a wheel can get, aesthetically. Some folks looking for more bling for their $1975–$2200 wheelset investment might not like the subdued appearance, but the look isn’t cheap or boring by any means.
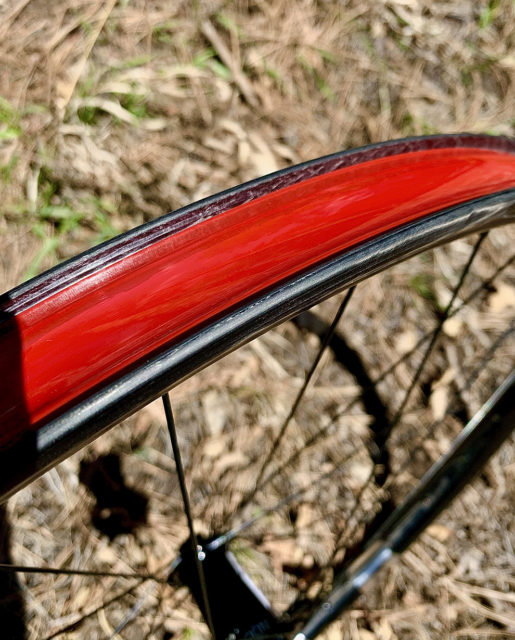
Build, Options, & Purchasing Details
The RW30 wheelset is laced and assembled in the same CSS facility that produces the rims in Gunnison, Utah. To fill out their full wheel builds, Revel has partnered with Industry Nine and Sapim to provide the hubs and spokes, respectively. There are two build levels, one using Industry Nine’s mid-level 1/1 hubs ($1975) and the other using the Industry Nine’s premium Hydra hubs ($2200). Regardless of which hubs you go with, both versions come with Sapim’s D Light spokes, and you can also buy the rims on their own for $699 apiece. Our review wheels came with the Hydra hubs.
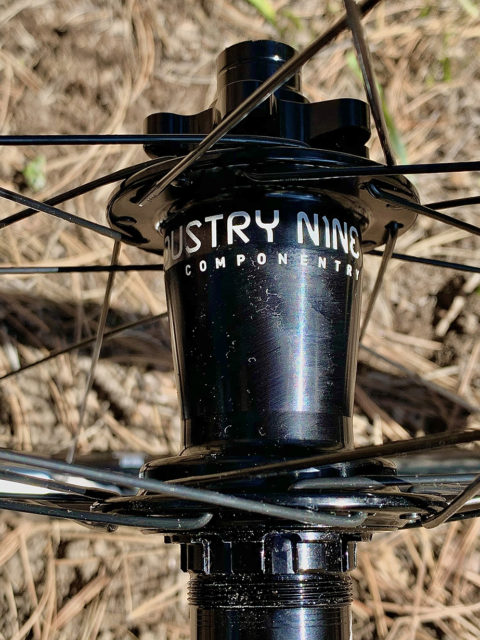
According to Industry Nine, “every step of design, engineering, manufacturing and assembly is done on premises to our exacting standards.” Admittedly, I do like knowing that Industry Nine controls their process from raw material to a finished hub in-house, just as Revel controls their rim manufacturing from raw Fusion-Fiber to finished rim.
Where things aren’t simple is the drive mechanism for the Hydra hub. Hydra uses a 115-point drive-ring engaged by six pawls. The pawls are purposely out of phase with one another, engaging the drive-ring independently. Normally, with in-phase pawls, a certain number of pawls would engage simultaneously. However, various forces through the hub – both from chain tension and frame/axle flex – causes small amounts of flex within the hub itself. This flex has the potential to lead to binding that results in pawls not engaging properly, adding stress to the hub bearings. Industry Nine says the Hydra hubs take advantage of this flex. With independently phased pawls, one pawl engages the drive-ring initially, and when the freehub body flexes ever so slightly, additional pawls catch up to the drive ring and engage. This is said to reduce bearing stress and increase durability. It also makes for one hell of a fast engagement at 0.52 degrees, besting their earlier premium hub — the Torch, which was considered very fast in its day — by 2.5 degrees.
All full Revel wheelsets are laced with 28 of Sapim’s D-Light double-butted spokes in a 2-cross pattern with Sapim’s black brass nipples. 32-hole rims are available for purchase, but for now, all complete wheelsets from Revel are of the 28-spoke variety.
Warranty
Like many carbon wheels, the RW30 comes with a lifetime warranty and a crash-replacement program for the original owner. If you break the rim, send the wheel back to Revel and they’ll send you a loaner wheel to ride while your wheel is either repaired or replaced. Then Revel will send your wheel back to you, with all shipping paid by them. Revel makes it a point to say that, in the event of a severely damaged rim, they want the rim back in order to recycle it.
Weight & Comparisons
Revel says one of their 29” RW30 rims weighs 480 grams. To put that weight into perspective, here are the stated weights for several other carbon and alloy 29” rims with similar internal widths in the Trail / Enduro category.
405 g Ibis S28 Carbon
408 g Enve M630
425 g We Are One Faction
480 g Revel RW30
490 g Santa Cruz Reserve 30
495 g We Are One Union
525 g DT Swiss XM 481
525 g Race Face ARC30
570 g DT Swiss EX 511
580 g Enve M730
618 g Stan’s Flow EX3
Receiving and Mounting
The RW30 wheels arrived in a single box with the wheels in plastic packaging bags with plastic end caps. In keeping with the recycling theme, Chris Reichel at Revel says they’re currently working on better ways to package and ship their wheels out to customers. FWIW, Revel doesn’t seem to just be talking about more sustainable shipping methods — right now, they ship their bikes out in a reusable EVOC travel bag that customers can either purchase along with their bike or send back to Revel to use again on another bike.
Once out of the box and packaging and with rim strips and valves installed, the RW30 front wheel weighed in at 859 grams and the rear wheel was 981 grams. In a boost for truth in advertising, this adds up to 1840 grams, which is the exact weight Revel publishes on their website for a 29” wheelset with the Hydra hubs. Nice.
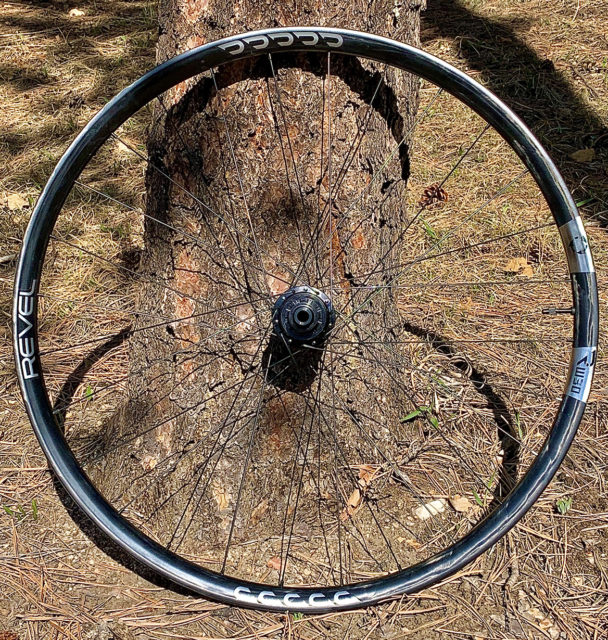
Putting six-bolt rotors on the hubs and installing my SRAM 10-50 cassette was straightforward. The front tire (Maxxis Assegai 29” x 2.5” WT Exo+ / MaxxTerra) mounted up with the trusty floor pump, no boost pump or air compressor needed.
The rear tire (Maxxis Dissector 29” x 2.4” WT Exo / MaxxTerra) was more finicky and required the air compressor. (Note: If you’re the type who changes tires and wheels even just a few times a year, a small air compressor found at the hardware store is a really nice tool to have.)
Fitting the RW30 wheels to the bike was even less eventful. Only a small adjustment of the front brake caliper was needed to prevent rotor rub.
Initial Ride Impressions
I now have a dozen rides on the RW30 wheels and some trends are emerging. That said, I’ll be updating this section over the next couple months as I get more time with the wheels and can A/B them against other wheelsets. Fellow reviewer Eric Freson also just recently started spending time on a Revel Rail 27.5” fitted with Revel’s RW30 wheels, so he’ll also be adding some of his thoughts down the line.
Thus far, the overall impression compared to other carbon wheels I’ve used is one of damping. That is to say, the RW30 wheels themselves feel significantly more damp than other carbon wheels — and alloy wheels — that I’ve ridden. It will be interesting to see if this observation continues as the review progresses. For now, when I enter a chunky section of trail, the RW30 wheels themselves contribute to a taught, more controlled vibration through the bike (I’ve been using them with my Yeti SB5.5). The suspension feels slightly more composed over sections of trail where, in the past, I would notice a bit of skittishness with super stiff wheels.
Contributing to this damp feeling is that the RW30 wheels are also quieter. This is a two-fold observation.
Firstly, the rims simply don’t make the sounds I’m used to hearing on stiff carbon rims or alloy rims. When a sharp impact occurs, the sound is more muted on the RW30. The best way to explain this sound is like a dull “thud” rather than a sharper, higher frequency “ping” or knock. This lack of sound was immediately noticeable during both smaller and larger impacts.
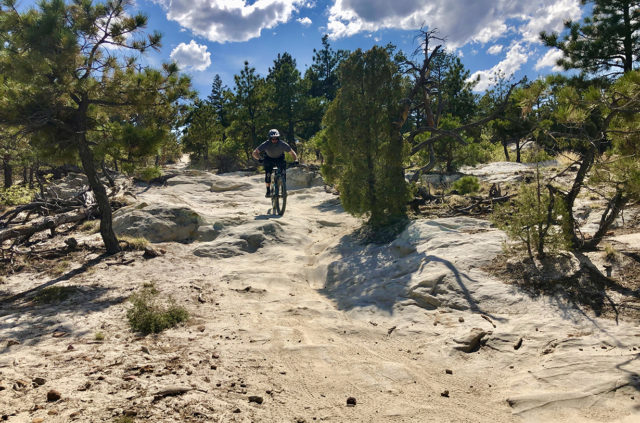
Secondly, when coasting, the Industry Nine Hydra hubs make a higher-pitch sound but at a lower volume than other premium hubs, specifically Industry Nine’s older Torch hubs or the numerous Chris King hubs I’d ridden in the past. Outside of the Onyx hubs with their sprag clutch, I personally haven’t heard a quieter, high-end hub than the Hydra. Bottom line: the material properties of Fusion-Fiber, in concert with quieter Hydra hubs, make for a very quiet ride thus far.
As for acceleration and cornering, for now, I can’t say that the RW30 wheels clearly stand out compared to other high-end wheelsets in the Trail / Enduro categories. This isn’t totally unexpected as the RW30 wheels, though fairly light, are comparable in weight to most other high-end Trail / Enduro wheelsets. That said, if you’re coming from average-weight alloy wheels, I’m confident you’ll notice a more nimble and quicker bike when pedaling out of corners, popping off trailside features, or in aggressive cornering. But if you already ride a high-end Trail / Enduro carbon wheelset, the RW30’s handling performance is, thus far, similar.
I don’t have much to write about regarding durability yet and we will have more time to draw conclusions before we update this review. But there is one initial observation that I wanted to talk about. On one of my first few rides, I dialed down the air on both tires to what I would consider an irresponsibly low pressure (18 psi), given my weight (180 lbs) and where I was riding that day. On that trail, there’s a small section where pre-hopping two small ledges at speed results in landing smack into a small rock ridge that has dented some of my alloy rims in the past. There was zero ambiguity about the hits the RW30 rims took on that section, but I found no damage on the rims and for now, they are still spinning true.
Another word about the Hydra hubs — the 0.52-degree engagement is noticeable in technical situations. Anytime I’ve been in a situation at low speed where careful balance + immediate torque is needed, the hubs have made a positive difference in my ability to claw through the situation. There was an annoying high-pitched rubbing sound coming from the front hub on slow, high-torque climbs that I initially chalked up to rotor rub. After tightening down the axle another half-turn and re-engaging the axle lever, I haven’t heard it in a few rides.
Some Questions / Things We’re Curious About
(1) Will the damp and muted ride qualities of the RW30 wheels be less noticeable as we spend more time on them and compare them to other carbon wheels, or will the RW30 still stand out in these regards?
(2) After extended time on the RW30 wheels, will any noticeable differences emerge in terms of acceleration or cornering vs. standard carbon wheels?
(3) Will the durability of the RW30’s thermoplastic material continue to be a highlight, or will I find the limits of the Fusion-Fiber rims?
(4) There is something potentially unsettling about a hub that is engineered to engage pawls due to driveline flex. Will we have any durability or maintenance concerns with the Hydra hubs after extended testing?
Bottom line (for now)
The Revel RW30 wheelset claims to do a lot of things. To make a more durable carbon wheel, with performance characteristics congruent with other high-end carbon wheels, and then make it the most easily recyclable carbon wheel on the market, well, it’s a lofty goal.
So far, Revel seems to be onto something. And what’s more, from a macro view of the bike industry, we have a feeling here at Blister that the Fusion-Fiber story is just starting to be written. Stay tuned for long-term review updates on durability and ride qualities.
From an engineering standpoint, “Fusion Fiber” is almost exactly the same play as Guerilla Gravity’s “Revved Carbon” (thermoplastic vs thermoset resin, robotic placement/layup, etc). As you say it sounds like a shamwow commercial but it has a long, legit track record in aerospace.
The main question I have is what resin they’re referring to when they say “think nylon, but on a whole new level”. The fashionable choices in aerospace and broader industries are PEEK/PAEK resins, and that’s what I suspect GG are using based on some things they said in the podcast, but that’s chemically not all that similar to nylon.
Replying to Patrick Chase.
To answer your question, other than in speaking about thermoset carbon, the word “resin” was never used in reference to the agent within the pre-preg that binds the fibers together in Fusion Fiber. The word “polymer” was used extensively. Whether or not polyether ether ketone qualifies as a resin or a polymer (or both) may be a matter of semantics from a consumer point of view.
That said, I’ll look into the this and get an answer if one is available. Understandably, the proprietary aspects of these materials are pretty hard to get here in the early going of their use in the bike industry.
Basically everything that is commonly referred to as a “plastic” and specifically everything that sees use as a matrix for carbon fiber (nylon, epoxy, PEEK, etc etc) is an organic polymer of some sort, so that strikes me as a distinction without a difference.
Traditional CFRP uses thermosetting polymers (i.e. ones that solidify via an irreversible chemical reaction, like epoxy), while GG and Revel are using thermoplastics (ones that solidify via cooling and can therefore be re-melted by heating). This is why the mold cycle times are so much better for thermoplastics – you need only cool the part down, as opposed to waiting for the reaction to complete. It’s also why thermoplastics don’t need to be refrigerated. You simply store them in solid phase, and heat them up to melt them when it’s time to inject. With traditional prepreg you actually have to keep the impregnated sheets cold to inhibit the solidifying reaction, and even then they can have limited shelf life. Note that a traditional flexible prepreg is more or less impossible with thermoplastics, though as it would have to be handled at temperatures above the plastic’s melting point. It sounds like they may be emulating the handling characteristics of prepreg by distributing small beads of solid thermoplaastic throughout the fiber or something like that.
Another interesting aspect of thermoplastics is the potential for repair. If a crack develops in epoxy you are hosed. If a crack develops in a thermoplastic you may be able to re-fused it by heating. The US military drove a lot of early research in the field back in the 80s/90s when they realized that their future combat aircraft would be largely composite, and that repairing battle damage was basically impossible with thermosets. They initially wanted to use thermoplastics for much of the F-22, but the technology just wasn’t there. Now it is, though I don’t know if it’s reached up into those ultra-high-performance niches yet.
Thanks in advance for any added details you can shake loose. As a former ME frI’m always curious about this stuff.
Exactly, when I listened to the podcast with Guerrilla Gravity, all I could think was: rims would be be a better use of thermoplastic carbon than frames
Yep. Impact resistance etc.
Yeah, I was reading this and thinking: If these wheels were put on a Guerrilla Gravity frame, would that be the most indestructible carbon bike ever?
Listening to Adam Miller was painful. He obviously doesn’t know much about induction welded thermoplastics. Defiantly a marketeer and not an engineer. Using pre-pregnant tape lay-up PA6/PA66 has been around for 30 years+. “Fusion Fiber” is cute. And PA6 (nylon) is the garbage of the thermoplastic world. What would have been interesting would have been for him to describe the void control process/management for the induction process. Or how they are doing quality control. Because it’s difficult to do on complex surfaces.
Holy nerd fest Batman!! Does anyone on this site actually ride bikes?
Where is updated info promised?
Njord…just ordered these wheels with Onyx hubs and I’m anxious to put them to that test. Interesting you bring up QC as I had just heard rumors out a southwest bike shop that there were some quality control issues. This is the first I’ve heard of it and I’ve searched the internet to find any articles to substantiate the rumor, but alas I’ve seen nothing. Every review I’ve read to date has been pretty glowing, but I’ve yet to read a truly long-term review.
I will check back in to see what others have to say and at the same time put miles on my wheels and put a review here.
Interested in ordering the exact setup you have with the Onyx vesper hubs. Any issues with either the hub or rims? Any notable positive qualities? I’m coming from an alloy set of i9 hydra wheels
Update?