From what we understand, with Flipcore construction, Blizzard makes a core profile in the ways described above, but places it in the rockered mold “flipped” 180 degrees so that the convex surface of the core (which traditionally faces up inside the ski press) is now facing down toward the base material.
This way, Blizzard claims, the final reverse camber shape of the ski is achieved without artificially bending the core against the mold, as in traditional methods. Rather, the ski’s reverse camber is literally built into the core. Both the bottom of the flipped core AND the mold have a convex, rockered shape to them, rather than just the mold.
When the materials are pressed together, the core itself is not bent or stressed. The core’s downward facing, convex shape is pressed against the identical convex shape of the mold. This produces the final “Natural-Rocker” shape of the ski.
What’s It All Really Mean?
Blizzard claims that because the Flipcore molding process does not bend or manipulate the core at all by making pressure adjustments to the press, the ski is produced with a more equal, smooth pressure distribution. The company states that Flipcore skis have “remarkably even flex characteristics and a flex pattern that marries perfectly with the sidecut and the rocker profiles.”
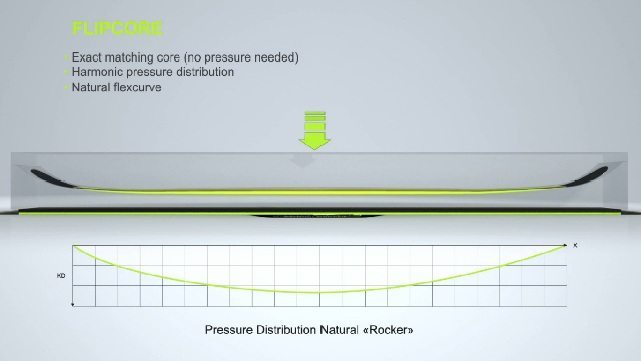
Blizzard’s Conor Brown notes that with Flipcore Technology the “[ski’s] material is in it’s natural state,” so that in a turn, “its natural tendency is to bend even more so you can push that radius of the ski because the ski just wants to keep bending.”
From what we gather, Blizzard seems to reason that bending a core into a rockered shape (by way of ordinary production methods) significantly changes the wood’s material characteristics, negatively affecting the way that core is allowed to flex and bend.
While we rarely care what BLISTER reviewer Joe Augusten has to say about anything, he happens to be a structural engineer; so we made an exception to our general policy regarding his opinions, and asked him to weigh in.
Joe explains that a material such as metal undergoes a process called “strain hardening” when bent, in which the molecular structure of the material is indeed altered and often times strengthened. However, this isn’t necessarily the case when working with wood during ski construction. Heat, along with other methods, can be used to remold wood without necessarily over stressing the wood fibers.
Profiled ski cores are usually around one centimeter thick at their widest point and very thin at the tip and tail. When the ski is molded, the relatively thin core’s wood fibers are not bent to the point of breaking or tearing, they’re simply forced to take a new shape. (If you were to take a popsickle stick, soak it in hot water, place a slight bend in it, and allow it to dry, you’d be replicating such a process.) The wood fibers remain continuous and intact, just as they were when the core was unbent, only they are now in a re-molded state.
In this new state, the wood is not under any additional stress; additional stress occurs only when the wood is flexed.
[A short aside: to be clear, when profiling a core, fibers are being cut as the wood is tapered. Ultimately, while continuous, the strands of fibers on the top of the core (traditionally speaking) are shorter than those running along the bottom as a result of the profiling cut.
This presents another interesting question about Flipcore. The shorter lengths of fibers are situated on the bottom of the core, and are put under direct tension when the ski is flexed. What sort of significant advantages or disadvantages does this orientation present compared to a conventional core?]
Now, back to bent (traditional) vs. straight (Flipcore) fiber structures in a ski core….
Interesting article. Makes some sense. I have been under the impression (actually, I was told) that in many ski companies, the camber is actually milled into the core, not just pressed in. While I understand that forcing it to rocker may break these fibers, if I’m not mistaken, then traditionally cambered skis are not being broken. This wastes wood, but helps prevent them from losing camber right away.
Can anyone comment on this? Is it wrong?
Good article. But as you seem to be saying, leads to more (good) questions.
Any chance the introduction of the bamboo core has impact on the properties of the ski than the flipcore construction? After all, ON3P uses bamboo exclusively and you pointed out the stability of skis from that manufacturer in your article. Liberty skis (amongst others) also use bamboo and have been picking up a host of industry awards lately.
I’d be interested in doing a test if Blister wants to help answer some questions. It would be fairly easy for us to lay up an stock Caylor, a ski that Blister has had some experience on, and just flip the cores. It wouldn’t be an absolute true test since the stock and new flipcore skis would have seen different riding conditions and use, but after a two or three day break in period, you could ski em back to back for comparison.
We’d definitely be interested, Rowen! As we say at the end of the article, this would be the best way to determine if we can ‘feel’ a difference, so this would be awesome.
Thanks for explaining this technology. I’m not sure if I understand though…If a core is turned upside down in the press, the press still forces the core to bend from a negative camber shape to a positive camber shape in the waist (since all flip core models seem to have positive camber). Here, the stress on the wood fibers should be increased, or not?
That’s what I was wondering…
You know what, those guys over at Blizzard are just lazy. One afternoon, after a long day of inhaling wood dust and fiberglass particles, the guy operating the ski press gave the dude passing him the profiled wood cores a look and said, “seriously? you really want me to push the wood against the direction it wants to go? do you know how much energy thats going to take?” Minutes later, Flipcore was born.
As an aside, the Cochise looks like a great ski.