The Spokes
While you can buy Industry Nine hubs with traditional flanges for traditional J-bend spokes, the I9 system wheelsets like the Enduro (both the version I tested as well as the new one) come with straight pull aluminum spokes. The spokes have a fairly large diameter (2.75mm at their narrowest), and there’s 32 of them holding the rim onto the hub on both the front and rear wheels. They’re laced in a standard three-cross pattern.
The aluminum spokes don’t use a nipple—rather, they thread directly into the hub. At the rim end, where the nipple would normally be, there are wrench flats that are sized for a normal spoke wrench.
At the hub end, there are threads external to the main body of the spoke, meaning that the threads aren’t cut into the spoke. Given that this is a high stress area, this is a good thing—the spoke actually increases in diameter (and therefore increases in strength) through the threaded area. Industry Nine has to machine down the rest of the spoke so that one little area has raised threads. Obviously not the easiest or quickest way to make spokes, but it gives you a stronger result.
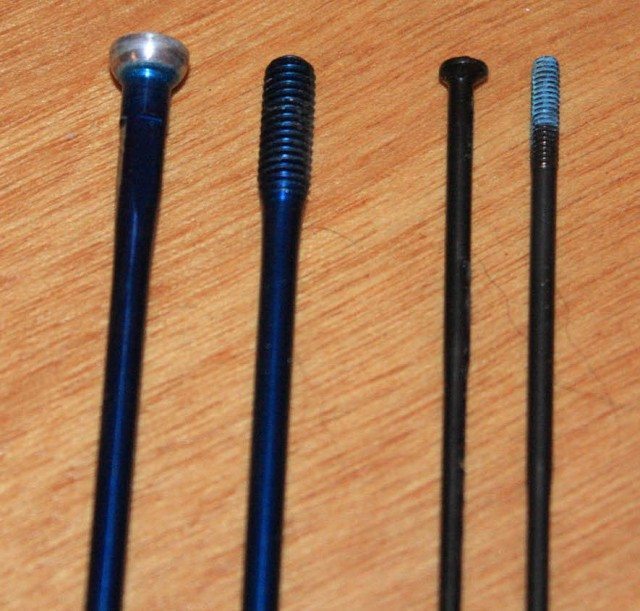
But, you might ask, don’t steel spokes work just fine? Sure, steel spokes get the job done, but the I9 spokes are lighter and stiffer. According to I9, their spokes have the same tensile strength as a straight 14 gauge (2.0 mm) steel spoke, but weigh about the same as a triple butted spoke (which I confirmed on my own scale). Additional weight savings comes by eliminating the spoke nipples—and that weight savings matters a bit more since it’s at the outer edge of the wheel. (More on that in a bit.)
While the aluminum spokes weigh about the same amount as a triple butted spoke, they produce a much stiffer wheel. In my experience, triple butted spokes are fine if weight savings is your top priority, but a wheel with triple butted spokes is going to be relatively flexy and won’t hold up well to rigorous riding. That wasn’t a problem with the Industry 9 wheels.
This is not to say that the aluminum I9 spokes are not without their disadvantages. First, the I9 spokes are proprietary, so if you break one, it’s unlikely your local shop will have a replacement in stock. My wheelset came with a few spares, but if you don’t have any spares handy, getting replacement spokes will likely involve a call to Industry 9.
Secondly, these spokes aren’t particularly inexpensive. Replacement spokes cost $6 each, so you better hope that you don’t break spokes very often. (As I’ll discuss below, I have yet to replace a spoke.)
The third issue is a bit more theoretical, but it inevitably arises in any nerdy discussion about these wheels. Are the aluminum spokes more likely to break? The short answer is “I don’t know.” My empirical testing was inconclusive—I didn’t have any issues with the aluminum spokes, but I’ve ridden plenty of steel-spoked wheels for similar periods of time without any issues, either.
On one hand, aluminum has a shorter fatigue life than steel and it’s brittler. When a wheel is ridden, the spokes are constantly being pulled and pushed, something that eventually fatigues the metal. At some point, that fatigue will lead to the spoke breaking. And because aluminum is more brittle, it’s theoretically more prone to cracking or breaking if something hits it.
All other things being equal, a steel spoke would probably hold up against impacts and fatigue better than an aluminum one. But all other things are not equal—the I9 spokes have a substantially larger diameter than their steel counterparts, meaning there’s quite a bit more metal in an I9 spoke than there is in a standard spoke.
For my purposes, the I9 spokes seem to hold up just fine. I’ve never replaced a spoke and I’ve never had to true my wheels.
Will the I9 spokes still be going strong in 10 years? Only time will tell. But in the meantime, they do look really cool. And if you’re still horrified by the thought of having aluminum spokes, you can buy the “regular” I9 hubs and lace them up with the traditional steel spokes of your choosing.
A Brief Tangent: Why Wheel Weight Matters
For those of you who have avoided reading anything about wheels, know this—weight on your wheels matters a lot because…
1) It’s rotational weight. When you’re accelerating, it takes more energy to spin a wheel up to speed then it does to get a frame moving forward. The heavier the wheel (and in particular, the outer circumference of the wheel), the more noticeable that effect becomes. The same goes for decelerating, although this tends to be less noticeable.
2) It’s unsprung weight (e.g. it’s not supported by your suspension). For your suspension to work, your wheel has to move up and down (tracking irregularities on the ground). When your wheel hits a big bump, the wheel moves upward and the suspension compresses. During that upward movement, the wheel builds upward momentum, and it’s the suspension’s job to control that momentum. A heavier wheel means more momentum, which means the suspension will have a harder time doing its job properly.
Everything I just said is pretty simplistic. But just remember that weight on your wheels is usually more noticeable than weight on other parts of your bike.
The Rims
My Enduro wheels are laced with a Stans Flow EX rim (29”). Since the Flow EX rim isn’t particular to the I9 wheels, I won’t spend too much time talking about it. And as I noted above, the newer I9 wheels come with I9’s house brand rim, which I haven’t ridden.
At a claimed 545 grams, the Flow EX is light for a rim of its width (25.5mm internal width). It’s a non-eyeleted rim, so it can’t take higher spoke tensions—which makes it more difficult to build a really stiff wheel. Stan’s also pushes the tubeless aspect of their rims, but I’ve found that the Flow EX rims don’t hold a tubeless tire quite as well as UST rims. A discussion of the details would probably get a bit wordy, but UST rims have a little ridge that helps lock the bead in place and prevent burping. I had issues with quite a few different tires burping air on the Stan’s rims.
All that said, the Flow EX’s are wide enough to give a nice square profile even with meatier tire options. While I only rimmed out a couple times, I didn’t have problems with the rims denting, and they stayed remarkably true during my time on them.
NEXT PAGE: Ride Qualities
“It’s also worth noting that each pawl has three teeth on it, so when a pawl engages, it simultaneously engages with three teeth on the drive ring rather than just one. This means that, whenever you’re pedaling, there are actually nine points of engagement on the drive ring.”
That design aspect is HUGE when it comes to freehub durability under low-rpm, high-torque pedaling. Great review. My takeaway? Industry 9 hubs = great, Stans rims = maybe not so much.
“It’s a non-eyeleted rim, so it can’t take higher spoke tensions—which makes it more difficult to build a really stiff wheel.”
You have a really slick site here, with lots of info to wade through. Unfortunately, in each article I’ve read (thus far) I’ve come across unsubstantiated myths that you seem to be perpetuating out of, um, ignorance? The quote above is a good example, and is patently untrue.
Please do your due diligence–which means stop repeating back-of-bike-shop old-wives-tales, and start using information that you can back up with facts.
Until then, this site will continue to fall under the category of ‘interesting fluff’.
Hey Mike,
I’m not going to pretend that I know more about this subject than you, and I suppose its something of an honor to have you commenting on this, even if it’s just so you can (perhaps rightfully) call me a dumbass.
So with that in mind, I think I can concede that what I wrote is, at best, somewhat imprecise. I do, however, stand by the notion that certain rim designs handle higher spoke tensions more effectively. I don’t think I’m going too far out on a limb to say that you can achieve higher spoke tensions on an eyeleted rim (all other things being equal).
So does that, in and of itself, make the wheel stiffer? No – I agree that the numbers say it doesn’t, at least under “normal’ loads. But a lot of wheels these days are getting ridden in a manner that places fairly extraordinary loads on them, and it seems both from my personal experience and from looking at what others are doing that spoke tension does play a role in how stiff the wheels are. The example I would point to is the Santa Cruz Syndicate, which experimented with lower spoke tension on their carbon wheels to allow some degree of compliance to aid in cornering traction.
So, coming around to the point, you (along with Sheldon Brown and most others that I’d consider reliable sources on the subject) say that wheel stiffness isn’t affected by spoke tension unless the spokes become completely slack (note that I’m also referencing your comment from my WTB i25 review). I’m not disagreeing with you on this point – rather, I’m saying that wheels that are ridden hard are more likely to see spokes that do go completely slack. And by ridden hard, I don’t mean guys that can put out a ton of wattage and power up a climb. I mean guys that are going bigger and faster on trail bikes than what we were seeing on downhill bikes 7 or 8 years ago. For those guys, higher spoke tension makes it more difficult for the spokes to go slack, and thus the wheel ends up being stiffer with that higher spoke tension.
If I’m riding the bike in a straight line or going around a corner at a moderate speed, will I notice this difference? No. But if I choose a crappy line and come hacking into a berm at a 90 degree angle, putting a ton of lateral load into the wheel, am I more likely to send the spokes into slackness, thus allowing the wheel to flex more? My experience says yes.
But I don’t intend to come across as some dipshit know it all; I’m just trying to come up with an explanation for what I’ve felt while riding. My explanation may well be wrong – I’d certainly be interested to hear your thoughts on my theory.
-Noah
Hey Noah-
Thanks for the quick comeback. Apologies if my initial response came off harsh–too much internerding this week, I guess.
Jobst Brandt (King of Curmudgeons!) wrote an in-depth treatise about ‘soft spoking’ *many* years ago, as did (if memory serves) Gerd Schraner. I don’t remember the science they did (not wired that way, personally) just that the end result was “No, it doesn’t work to soften the ride in any plane’.
I’d be curious to read what the SCS came up with, and if there’s any real science behind it. My $02 is that if you hack/slam a berm hard enough to slacken the spokes, you fold your wheel. There *are* degrees of slack, of course, but I cannot imagine (given current rim and spoke tech) a situation where tension is being used to ‘tune’ the response to that, such that you can feel compliance. Changing the gauge of the spokes can do it to some extent, changing the crossing pattern can to a lesser extent. But ‘tuning’ it with tension to allow Rat and Minnaar to slay berms ‘compliantly’?
Color me very, very skeptical.
Cheers,
MC
No need to apologize – just a good discussion of wheel nerdery.
Here’s the link to the interview where the syndicate team support manager is talking about spoke tension. Unfortunately its a bit light on details (and sorry, hyperlinking doesn’t seem to work in the comments):
http://www.mtbvt.com/archives/20000
So I’m speculating that wheels that are getting punished will experience enough flex that the spokes (or, more accurately, one, or maybe a few spokes) go slack for a brief moment, which in turn allows the wheel to flex (more). It seems to me that, with a higher spoke tension, the rim would need to deflect farther before the spoke experienced a complete detensioning. So under “normal” loads, the rim isn’t deflected anywhere near enough to completely detension the spoke, and therefore spoke tension doesn’t make an appreciable difference. But under abnormal loads (which, for some riders, aren’t actually that abnormal), the higher tension would mean that the rim would have to flex farther to detension the spoke, and therefore in all but the most extreme examples, the wheel would be stiffer because the spokes experience a complete detensioning less frequently.
To put it another way, a wheel that has almost no spoke tension feels laterally flexy. The reason (I think) is that normal loads will easily detension the spokes, thus removing much of the support for the rim. With higher tension, this doesn’t happen under normal loads; the loads aren’t sufficient to fully detension the spoke. But at some point, it’s possible to reach a load that will once again start to detension the spokes, and in that case, the wheel again starts to feel flexy.
In support of this theory, here’s a few videos of wheels taking a lot of load. I *think* that in each of these videos, you can see that the rim is deflecting sufficiently so as to momentarily detension some of the spokes. And it would seem that, if the spokes weren’t completely detensioning, the wheel would fare better.
Or, you might say these videos don’t show anything of the sort and I’m full of it, in which case we can still go home happy because at least we got to watch some cool slow motion. Either way, I’m interested to hear your thoughts on this.
Videos:
1) Gee Atherton, going huge at Rampage. Maybe not the best example since this is pretty far outside of the scope of normal riding, but the impact on his rear wheel is significant.
http://www.redbull.com/cs/Satellite/en_INT/Video/red-bull-metro-pipe-2012-teaser-video-021242946727819
2) Giant Trance X 29 Teaser. There’s a good shot a :09 of the wheel flexing and popping back into line. I’m speculating that the spokes are (briefly) completely detensioning there.
https://www.youtube.com/watch?v=r_wKLlUjkiU
3) The cobbles of the Paris Roubaix. A slightly different context, and I’m not sure the spoke actually goes completely slack, but regardless, it’s a cool shot:
http://www.youtube.com/watch?v=W1QXKjc1nLY&t=2m2s
Good to see you guys playing nicely on the interweb. Too rare these days. I could make a science/engineering argument that spoke tension doesn’t affect wheel stiffness (mostly spoke strength, rim strength and hub strength instead), but nobody is likely interested in a bunch of stress/strain curves, Young’s Modulus recitations, etc., etc., this morning.
Or, I could trot out the e-world’s famous “simple physics” except I’m a reasonably bright guy, and still remember physics as being quite challenging.
I suspect the real truth is that once you get spoke tension to a certain reasonable level, going beyond that point yields no further benefit in wheel stiffness.
And Mike, while I share some of your suspicions regarding what pro riders can and cannot feel, I’ve been surprised before in “other” worlds, personally knowing both a pro auto racer and pro motorcycle racer that could each tell you if you messed with the air pressure in their tires by even a small amount.
Finally, to the point of Noah’s article, the only thing truly wrong with I9’s hubs is that they don’t yet offer them in Trek’s new (arguably ridiculous) 148 spacing.
Noah-
Thanks for the links.
Hatfield’s assertions seemed to largely be centered on avoiding answering the questions posed. Sometimes racers and their staff are cagey about answers to preserve secrecy and perceived advantage, but in this case it didn’t feel that way. Just felt like he didn’t know.
I’m writing this on a plane, thus I can’t watch the vids you’ve linked. But from your verbiage I think I’m clear on what you’re driving at.
My point is not that spokes going slack means immediate wheel failure. Surely one or two spokes can go completely slack several times per ride if punished enough. All this will likely mean is a few minutes with a spoke wrench–no biggie. Does that slackening affect the feel of the wheel? Sure–and I’m willing to bet most people that are pushing their own limits have felt this. Old-school friends refer to it as ‘sproinging’ the wheel–and it’s unmistakable because the wheel will give to a point and then snap *harshly* back into shape. I’ve done it many, many times through the years, usually when pushing hard on an XC bike and unceremoniously blowing a line. Always on a dished wheel, never on anything dishless. Curiously, I’ve never (yet) done it on a carbon-hooped wheel, and am somewhat skeptical that the SC boys are either. I write that because I’ve built and ridden enough ENVE wheels to know how inflexible and uncompliant they are, even in 29″. I believe most of us could ride ENVE rims laced radially with dental floss and not know a difference from the 2mm spokes that should be in their place. Just unyielding is the best way to put it. Like riding manhole covers. Aggressive riders on long travel bikes seem to appreciate them most. Hardtail and full rigid riders seem (generalizing, obviously) to hate them. Both reactions make sense to me, given my experiences with them thus far.
Back to the point, take one of the most unyielding hoops ever known to a bicycle wheelbuilder, and lace it any way you want–2x or 3x, butted or straight gauge, 80kgf (considered by most as very, very loose) or 150kgf (tzight!) and the end result is the same: That wheel is just as unyielding in every plane. I do not have machines to measure the resultant lack of deflection, but I’d wager a good meal that the difference in these builds (with final tension as the only variable) would be undetectable to all but the most precise measuring devices.
That, and one of my long-held contentions is that there are so many other things happening (knobs squirming, casing deforming, loose soil being scraped off, pebbles rolling under the tire, knobs ripping off, crosswinds, angle of the dangle, etc..) while riding that although we as riders can definitely feel differences from bike to bike and setup to setup and run to run, we can never be sure *exactly* what to attribute them to. What Hatfield asserts but never proves is that tension is making the difference. I’d wager that the placebo effect is just as likely to be the root cause. They’re in the business of winning races–can’t fault them for pulling out all the stops.
Regardless of these assertions, I cannot say definitely that I *know* that things are (or are not) working in this way. I *think* that the small angle from hub to rim, coupled with a theoretical understanding of how bicycle spokes work in tension, ultimately means that tension variances alone cannot be used to tune the ride. Tension variances *definitely* change the feel of a wheel, in the same way that tightening a guitar string produces a different tone. Vibrations feel different coming through a tighter spoke (string) than a looser one. But changing the feel is a long, long ways from changing the ride.
Your turn,
MC
Mike – that’s a pretty damn good response, particularly the last paragraph. It makes me wonder: to what extent does higher tension make the wheel “feel” stiffer, even if the wheel is not actually any more resistant to flexing. Obviously that would likely depend on lots of variables, not the least of which is the type of rim, but it seems like that would be a likely source of the “old wives tale” that higher tension = stiffer.
Distinguishing feel from stiffness is a good way to put it, and I’d add to that equation strength – quoting Brandt: “for greatest strength, spokes must be as tight as the rim permits” (he adds some caveats, but I’ll gloss over those for the sake of simplicity).
So, like I indicated in my first response, I can certainly concede that the review as written is imprecise. It’s probably more accurate to say that wheels with a lower tension will feel different, they’ll potentially be a bit weaker, and there might be some effect on stiffness but that effect is likely undetectable in most, if not all, scenarios.
Does that seem reasonably accurate?
Regardless, thanks for commenting – I appreciated the discussion. If nothing else, it got me to go back and re-read a chunk of The Bicycle Wheel as well as some other writings on the subject. And it gave me an excuse to hunt down a few slow motion videos of wheels getting thrashed, which, all things considered, is an enjoyable way to waste some time.