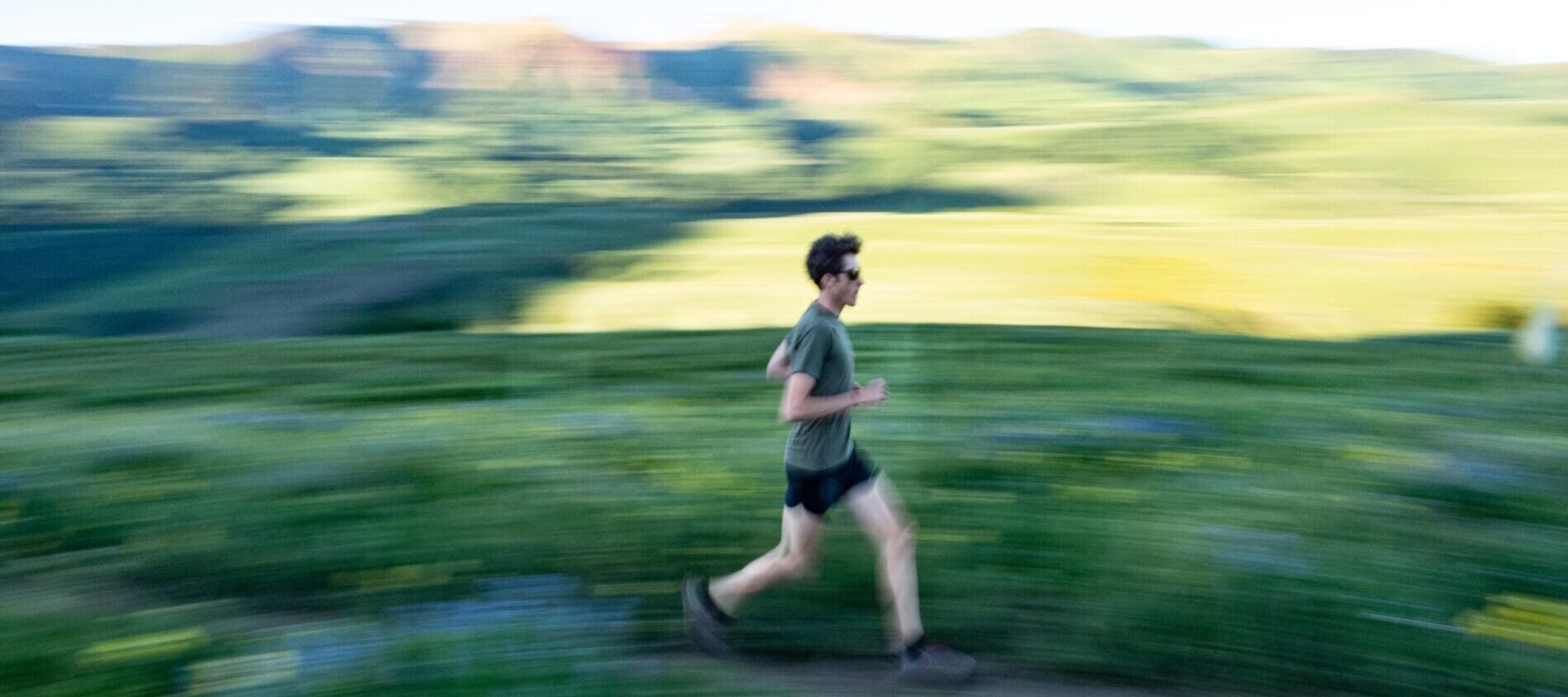
Intro
As the sport has continued to grow, true advancements in trail running shoe technology have been made in the areas between durability, weight, strength, price, and sustainability. These five elements rely in their own ways on materials — textiles and plastics, fabrics and foam. Most brands will highlight the components used to build their shoes but will wrongly assume that every runner knows what to do with that information and why it does — or does not — matter.
In our second installment in our Trail Running Glossary of Terms series, we’ve put together a list of some of the most common materials used to construct shoes, along with some of their benefits and drawbacks.
It’s important to note that the implementation of many of the terms below is not consistent across different brands or even models from the same brand. E.g., some form of “EVA foam” is used in hundreds of different shoes, but the EVA foam used in one shoe’s midsole might feel and perform wildly differently from another’s. That said, this should give you a basic idea of how to comb through all the marketing claims you see being made about this shoe or that shoe, and figure out what might actually be useful to you.
For a more general rundown on the construction elements of most trail running shoes, check out our Glossary of Terms for Shoe Anatomy.
(And if you’re having trouble deciphering a given brand’s shoe-tech jargon, be sure to check out our Running Shoe Brand Guides, where we go over every shoe in a brand’s lineup and discuss how each one differs.)
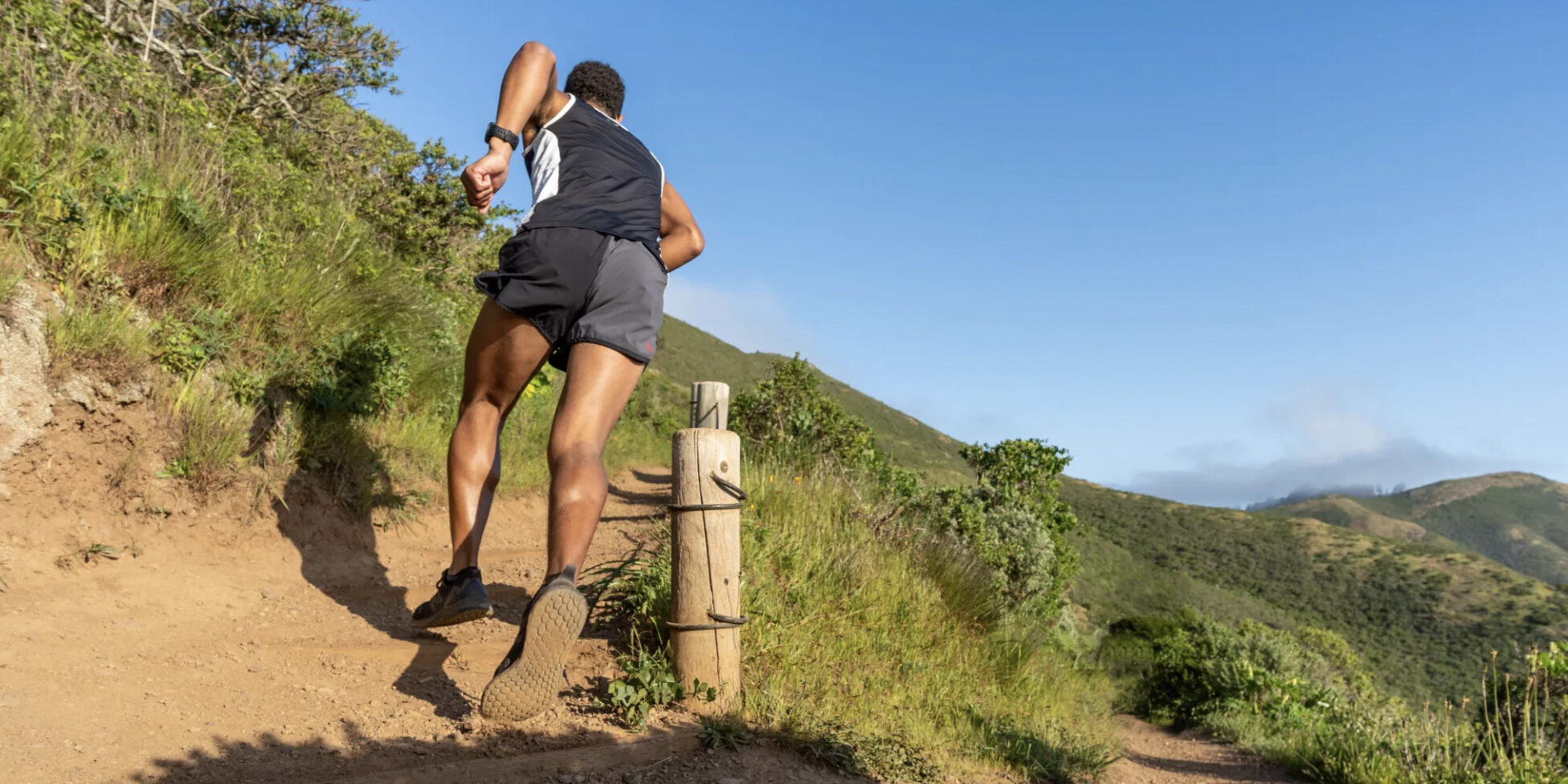
Common Upper Materials
Cordura: The Cordura fabric brand name encompasses a wide range of typically nylon fabrics known for their high tensile strength fibers. Cordura fabrics are generally water repellant, abrasion resistant, and come in a variety of weights / weaves. Running shoes sometimes make use of this material in uppers, for better durability and protection relative to the often softer, stretchier knit fabrics.
Matryx: A performance textile used in higher-end trail running models from a few brands. Matryx fabric is made from woven polyester threads that are individually coated with protective coatings. It’s known to be incredibly resistant to abrasions, flexible, light, and quite breathable (especially relative to traditional burly fabrics like Cordura). Performance-oriented trail shoes will incorporate Matryx by weaving it directly into their uppers or using it as a lightweight alternative to TPU for protective / supportive overlays.
Dyneema: Technically, Dyneema is an ultra-high-molecular-weight polyethylene. Dyneema (also known as ‘Cuben Fiber’ or ‘UHMWPE’) is known to be incredibly strong, abrasion resistant, and lightweight, and can be utilized in the form of fibers, yarns, woven fabric, and non-woven, laminated fabrics. It’s not yet widely used in trail running shoes, but as the technology and production cost become more affordable, expect it to be featured as part of new upper materials. Some brands that are currently taking advantage of Dyneema (e.g., Speedland) utilize the material in upper fabrics or even as a thread to reinforce the midsole-upper connection, due to its high level of durability.
Gore-Tex: A waterproof Teflon membrane used in some waterproof versions of trail running shoes (and a whole bunch of other products). Gore-Tex materials block liquids and air while allowing some vapor from sweat to pass through, but a shoe with a waterproof laminate will neither drain as well nor breathe as well as an equivalent shoe without one.
While many brands opt to use a name-brand Gore-Tex insert for their waterproof shoes, many others use different membranes, but the idea is similar. Weatherized versions of trail shoes also tend to keep feet warmer in cold conditions than shoes without a waterproof lining, so models outfitted with Gore-Tex and the like can be a popular choice for winter running.
‘Engineered Knit’ Fabric: While the vast majority of shoes’ uppers consist of some sort of knit fabric, recently, more complex knitting processes have allowed shoe designers to incorporate several different functions into a single piece of material, which can allow them to more precisely decrease stress points, reduce weight, increase durability, and maximize breathability. Some “engineered knit” uppers also don’t need to be trimmed, resulting in less waste during production. Constructing uppers from a single piece of fabric also eliminates seams, adding comfort by decreasing the amount of internal stitching needed in the shoe.
Kevlar: A synthetic, strong, heat-resistant fiber that can be woven into flexible sheets and used in overlays and uppers. Kevlar’s strength-to-weight ratio is nearly 5 times stronger than steel, which makes it a great option for reinforcing higher-end trail shoes designed for rugged terrain.
Aramid Fiber: This is actually the same exact thing as Kevlar; Kevlar is just the trademarked brand name of this light, strong, heat-resistant fiber.
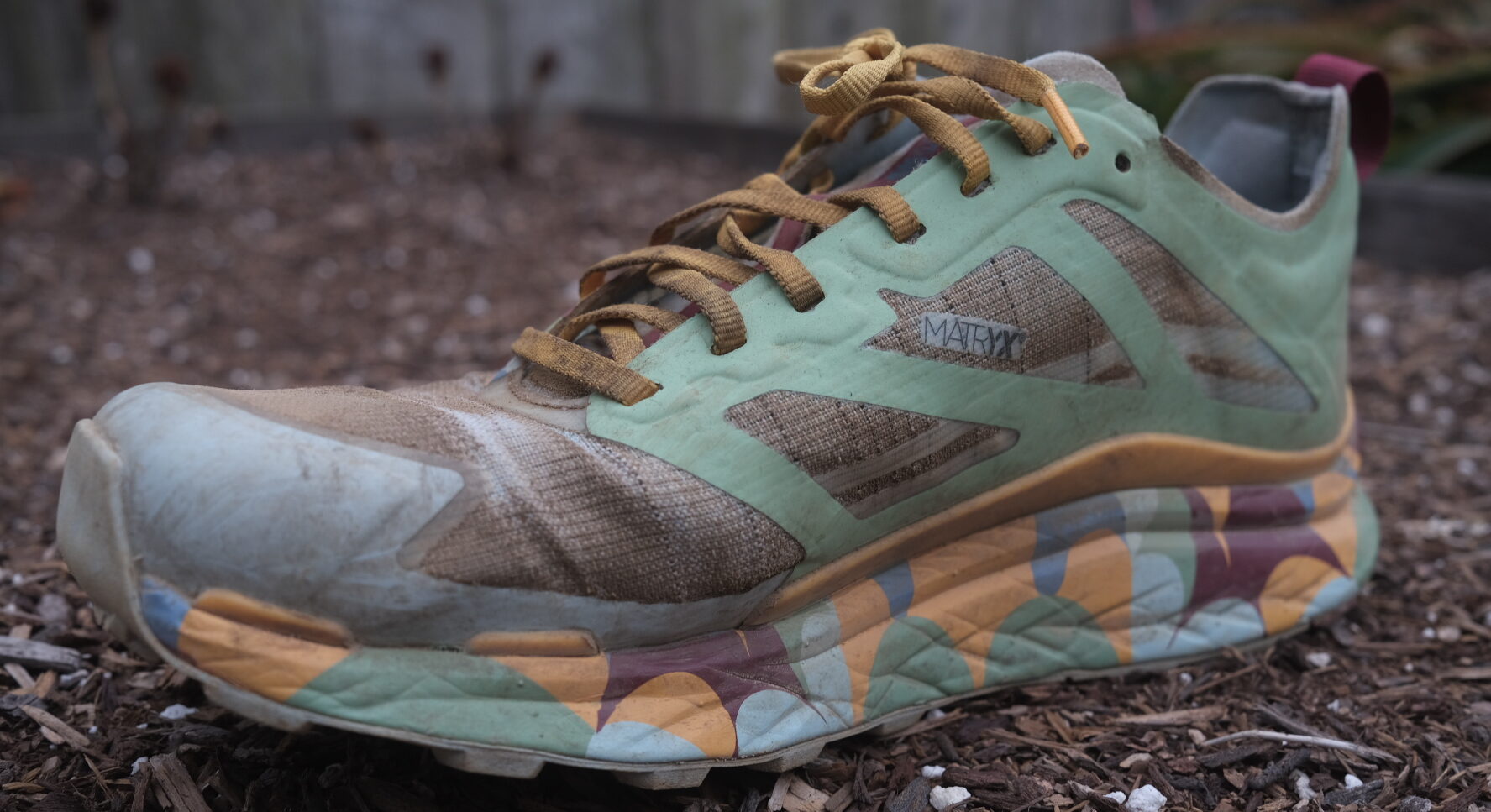
Common Midsole Materials
EVA: Otherwise known as “Ethylene Vinyl Acetate,” EVA combines two types of plastics to resemble a foam-like material. Most shoes’ midsoles employ EVA because of its balance between cushion and energy return. It’s also fairly flexible, easy to work with, and can be dyed different colors. Weaknesses of EVA include its temperature sensitivity — in colder conditions, EVA is known to firm up significantly — and its susceptibility to compression after prolonged use. On the whole, lower-density (softer) blends of EVA will have a shorter lifespan than higher-density (firmer) ones. While not as common in trail shoes, some footwear brands also use EVA in their outsoles instead of rubber to save weight. In addition to being lighter than rubber, EVA outsoles will generally absorb impact better than harder rubber compounds; however, they probably won’t provide as much protection on rougher terrain, don’t provide as good of traction (especially on wet / slippery terrain), and are more susceptible to abrasion.
TPU: The abbreviation of “Thermoplastic Polyurethane,” TPU midsoles in running shoes are typically made from fused plastic pellets. TPU is considerably more durable than EVA, despite comparable suppleness and energy return. It also maintains consistency when exposed to temperature ranges, but does all of this at the cost of being slightly heavier than its counterparts. TPU’s use in midsoles came in response to some of the longevity issues faced by midsoles relying on EVA, namely their tendency to degrade quickly and lose energy return. Today, most brands have their own proprietary take on TPU midsole compounds, though Adidas and their “Boost” material is widely credited as the first example of a brand making wide-scale use of the material in running shoes.
Pebax: The brand name for a popular type of thermoplastic elastomer / plastic called polyether block amide (PEBA), Pebax is now being used in performance-oriented trail running shoes both in the form of plates and midsole foams. With more flexibility than carbon fiber, Pebax plates and foams tend to better suit the demands of uneven trail surfaces, while still offering some of carbon’s increased efficiency / energy return. Compared to TPU-based materials, Pebax is reported to be significantly lighter, delivers better energy return, and likewise maintains the same performance across temperatures; however, like EVA, Pebax likely won’t be as resilient as TPU over time.
“Dual Density” Midsole: Refers to midsoles composed of two types of foam with differing densities. Multi-density midsoles are constructed to reflect the foot’s movement through the gait cycle, with softer materials typically placed at points of contact and more rigid ones placed along areas typically in need of more support. Motion-control shoes often feature dual-density midsoles to correct pronation / supination issues. In these models, a denser section of midsole is positioned near the arch on the shoe’s medial side to limit the degree to which the foot can collapse inward while running. This component is widely referred to as a “medial post” and can be made from EVA, TPU, or other materials.
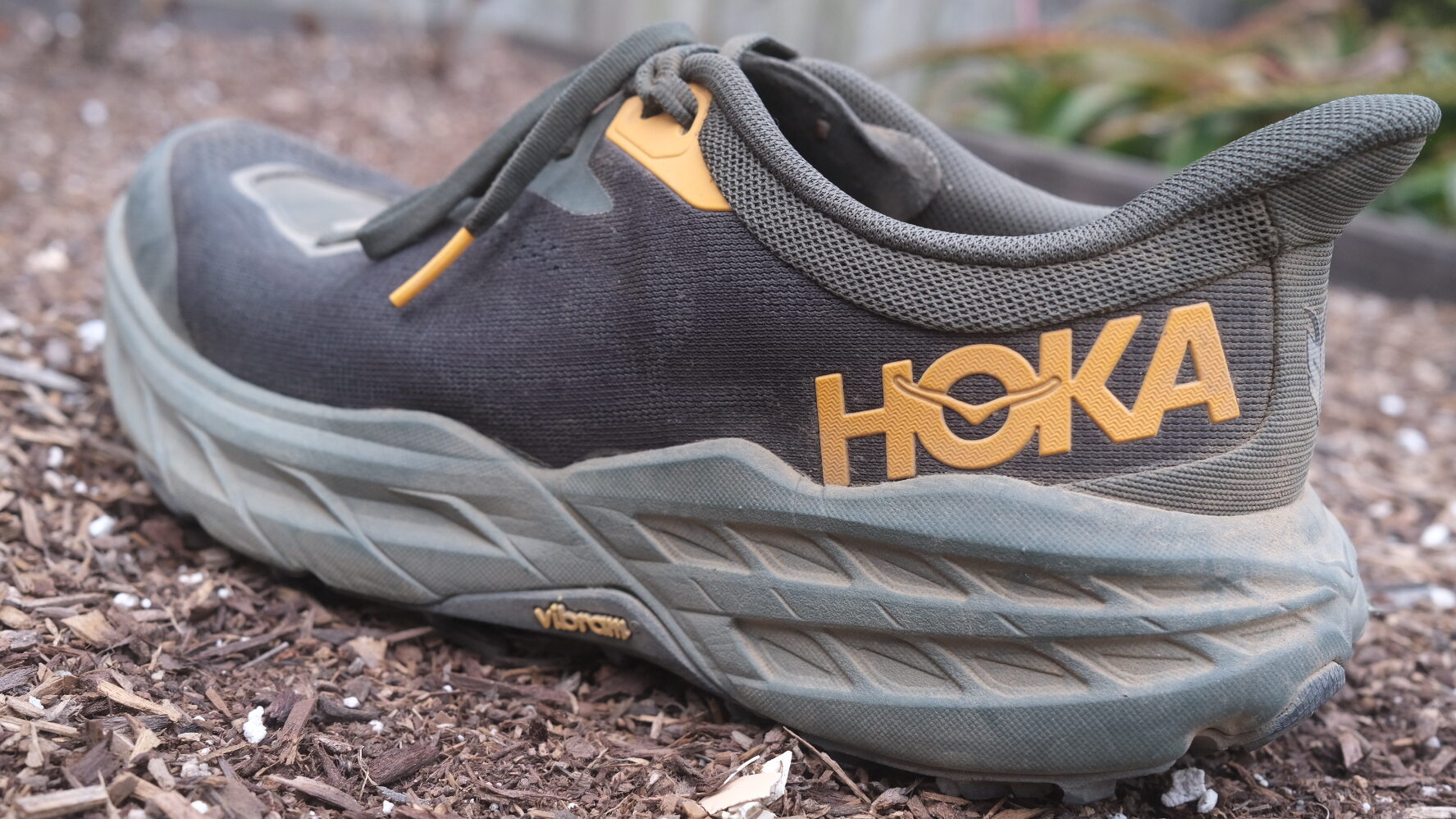
Common Outsole Materials
Vibram: Just as Gore-Tex is to waterproof fabrics, Vibram is to rubber outsoles, with many higher-end trail running shoes utilizing Vibram’s rubber compounds and/or tread patterns on their outsoles. Vibram makes a huge range of different compounds and treads, but two pieces of Vibram tech you often see in trail shoes include:
- Litebase: Refers to versions of Vibram outsoles that are notably lighter and thinner than Vibram’s other options (reportedly 30% lighter, 50% thinner). Litebase is commonly found on trail shoes designed for faster paces.
- Megagrip: Vibram Megagrip outsoles use a higher-end rubber compound that’s quite soft and designed to provide very good grip on slippery surfaces, but with less of a compromise in terms of durability, relative to many similarly grippy rubbers. Vibram makes two different Megagrip compounds, “65 / 70 Shore A” (a softer rubber) and “75 / 80 Shore A” (a firmer rubber). Different hardness formulas affect grip and durability. In general, harder rubbers tend to provide less traction than softer compounds, but what they lose in grip they make up for in resistance to wear.
Graphene: Graphene is an ultralight material that’s been used in many industries due to its excellent weight-to-strength ratio, but Graphene’s application is still relatively new to the running industry. Because it has tested 200 times stronger than steel (relative to weight) and is one of the thinnest materials on the planet (consisting of a single layer of atoms), shoe designers have experimented with infusing outsole rubber and midsole foam with Graphene to enhance durability without losing elasticity. Inov-8, the brand responsible for pioneering the use of Graphene in trail shoes, contests that their Graphene outsoles are 50% stronger than those using standard rubber compounds, and their midsoles enhanced with Graphene provide up to 25% more energy return compared to traditional foams.
Proprietary Rubber Compounds: Most shoe brands have their own names for their own rubber compounds (as opposed to a 3rd party brand like Vibram). Common examples include Salomon’s Contagrip, La Sportiva’s FriXion, and Altra’s MaxTrac. Proprietary rubber compounds and outsole patterns vary drastically and it’s not as easy to make on-paper comparisons between them, but it’s always worth checking a brand’s website to see if they offer details on how their compounds and outsoles differ from each other. E.g., La Sportiva offers useful info on their various proprietary “FriXion” rubber compounds.
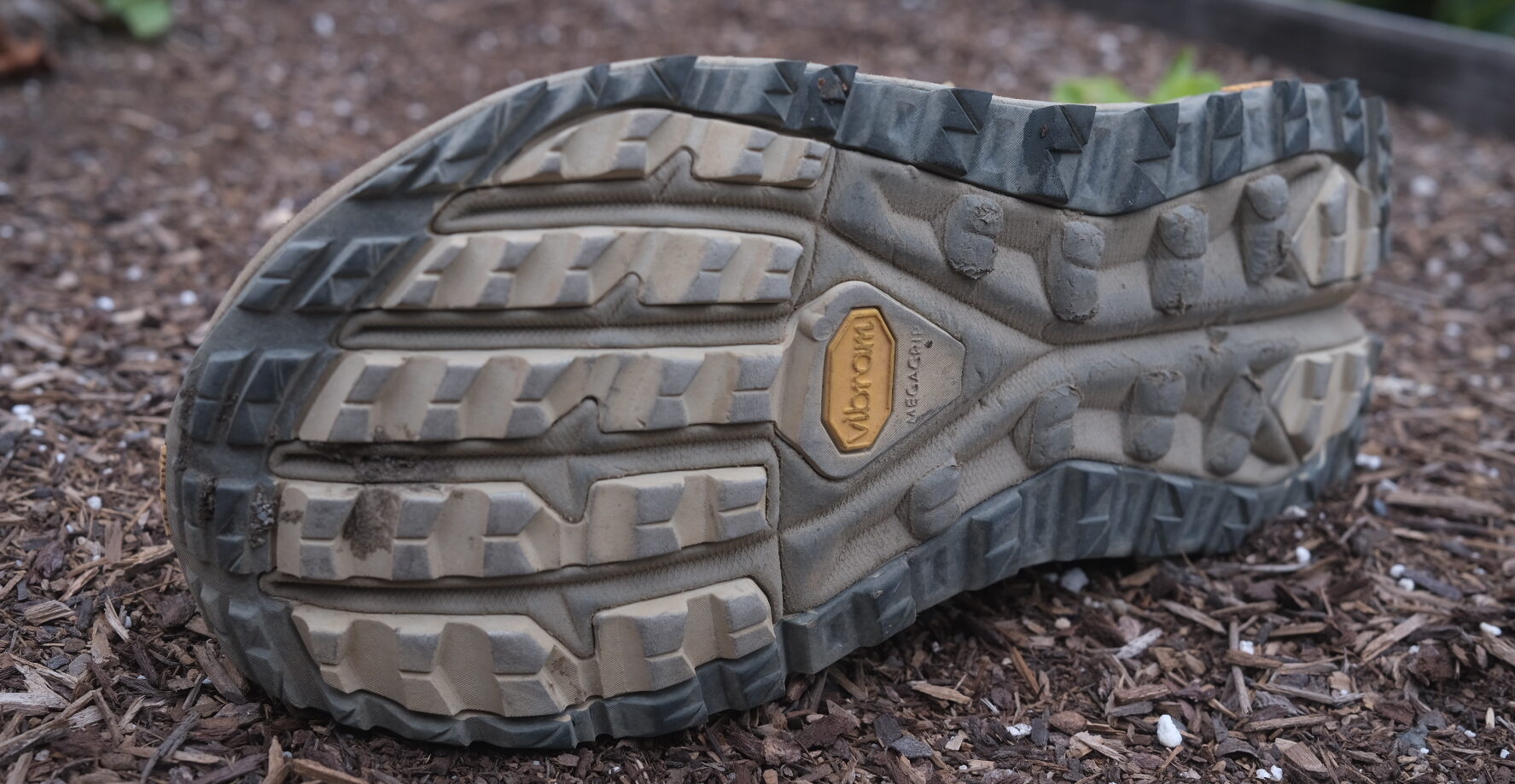
Alternative Lacing Tech
BOA Lacing / BOA Fit System: An alternative to threaded laces, BOA systems rely on multidirectional dials to adjust the tension of cables that run across the foot. While this style of lacing is pervasive in the cycling world, it’s just starting to migrate over to trail shoes in a serious way. Models outfitted with BOA systems allow runners to adjust fit quickly and precisely on the go and eliminate the threat of laces coming untied during activity. However, precision can suffer in models using only a single dial. Maintenance / replacement is also something to keep in mind vs. traditional laces. For more on BOA, check out Ep. 75 of our Off The Couch podcast, where we talked with two of BOA’s biomechanics.
Quick Lace System: Another alternative to traditional laces, quick lace systems make use of a single cord that’s threaded back and forth across the top of the foot and secured by a single pull-tight synching mechanism near the tongue. Fit can be adjusted by slackening or tensioning the plastic stopper that slides up and down the lace loop. Like BOA lacing, quick laces allow fit to be tweaked on the go and are much more secure than shoes that need to be tied manually. However, because quick laces are fixed in place and tightened uniformly from a single point, the ability to practice more precise, alternative lacing techniques (e.g., skipping an eyelet or tying a runner’s knot to prevent heel slippage) is lost.
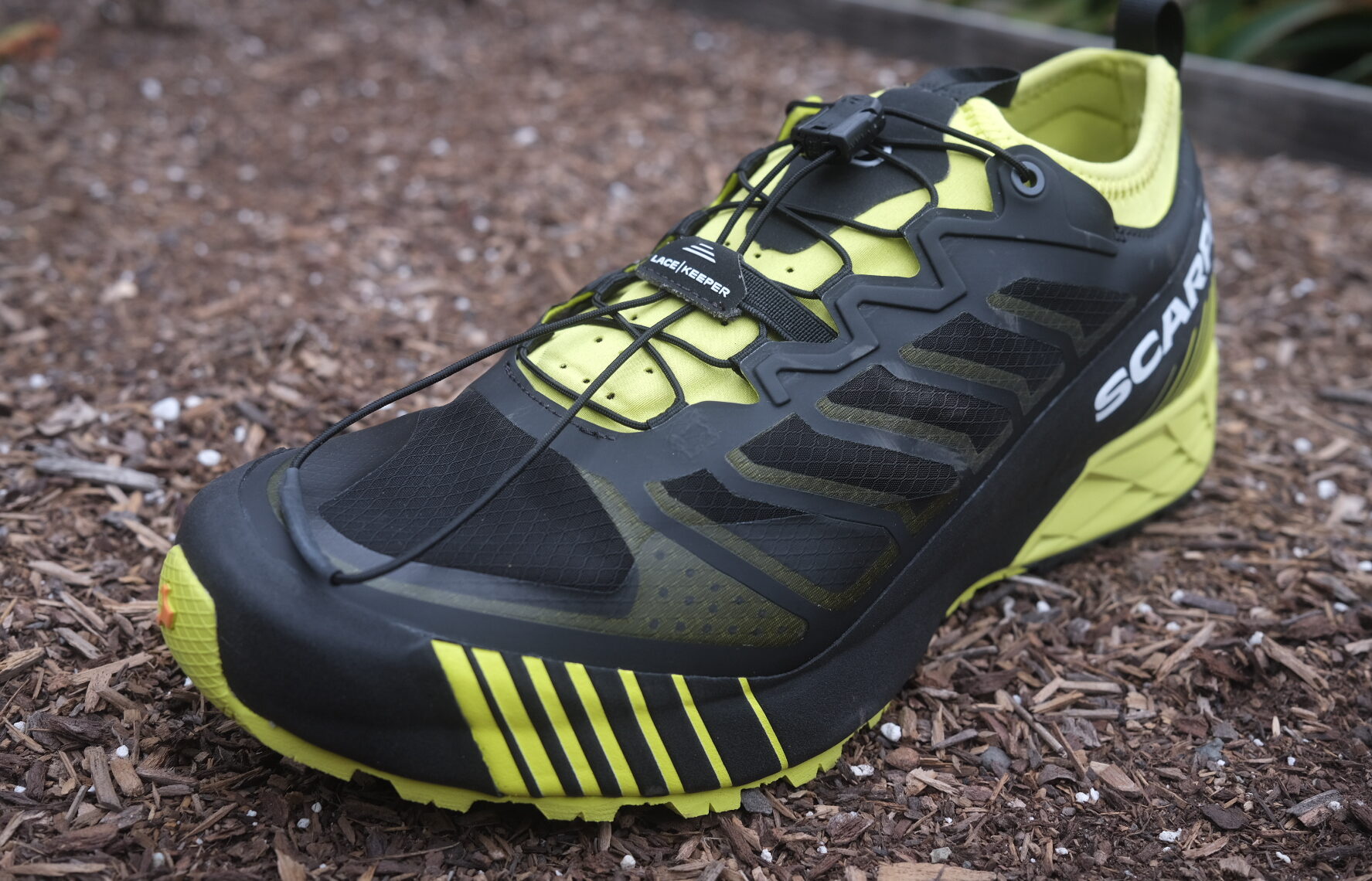