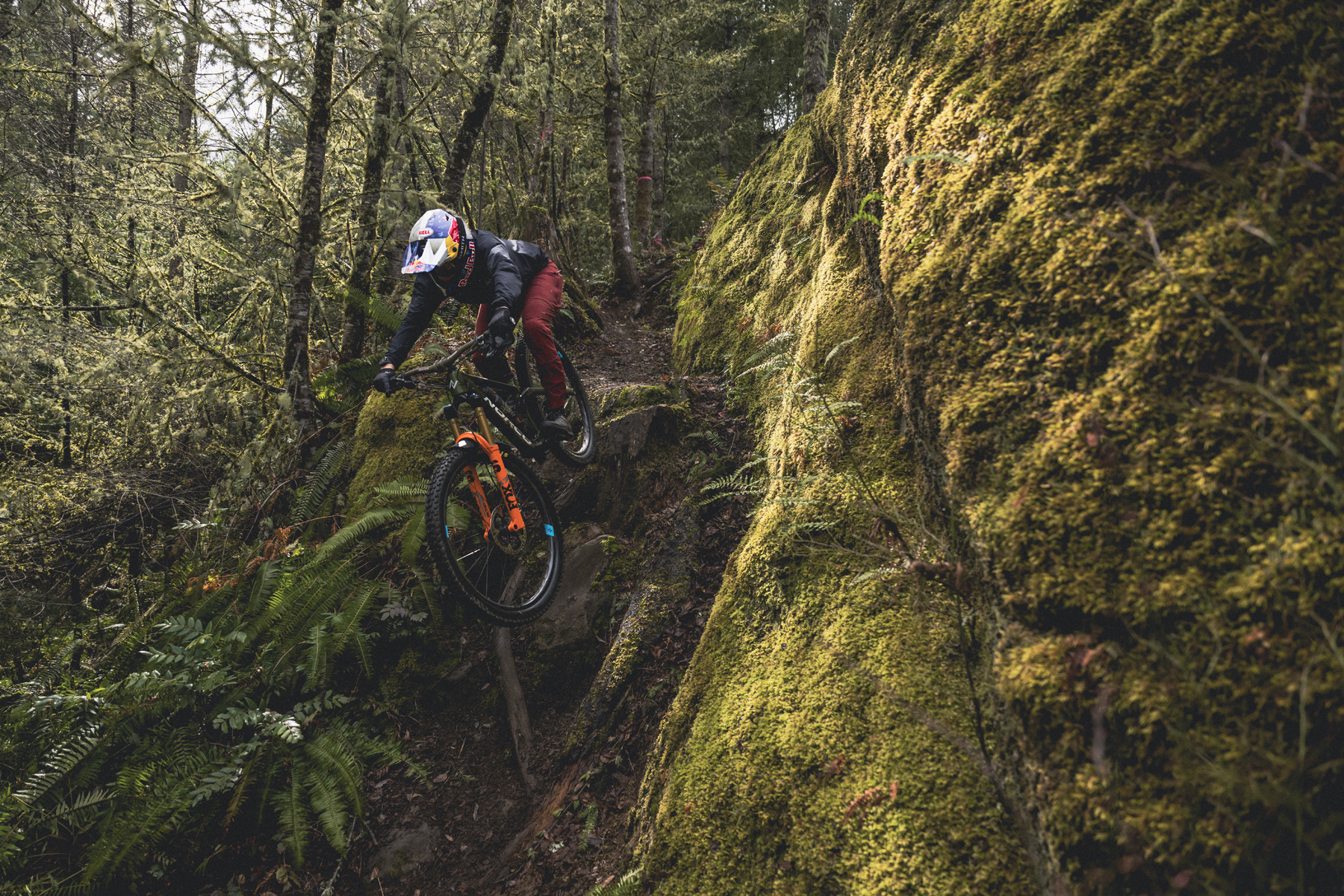
Designing, prototyping, testing, and refining a carbon fiber wheel is deceptively complicated. Things like weight, stiffness, vertical compliance, and durability are the standard buzzwords for talking about a new wheelset, but how do you strike the right balance between all of them, and how do you go about validating a new design? And what how does athlete feedback factor in, especially considering that the needs of top-level pros aren’t exactly the same as those of mere mortals?
We sat down with Kell Kirby and Travis Tomczak of Forge+Bond, as well as F+B athlete Jill Kintner to talk about all of that, and along the way, we get into the differences between thermoset and thermoplastic carbon fiber, why Forge+Bond uses the latter when the vast majority of carbon wheels (and other carbon fiber bike parts in general) take the thermoset path, and a whole lot more.
TOPICS & TIMES:
- The founding of Forge+Bond (2:29)
- Travis’ role (3:44)
- Kell’s intro & roll at Forge+Bond (6:10)
- How Jill got involved (7:48)
- The vision for Forge+Bond (9:35)
- Why thermoplastic carbon fiber and what is thermoplastic carbon fiber? (15:58)
- Why aren’t thermoplastics used more widely in the bike industry? (18:05)
- Where do you start designing a wheel? (20:57)
- Jill’s feedback and the role of athlete testing (30:39)
- Forge+Bond’s design philosophy (35:43)
- How to iterate on a design (39:45)
- Learning from prototyping (42:15)
- The current Forge+Bond product line & the recyclability of carbon fiber parts (46:33)